Permanent magnet synchronous direct-driven motor bearing structure of the stirring industry
A permanent magnet synchronous and motor shaft technology, which is applied in the direction of electric components, casings/covers/supports, electrical components, etc., can solve the problems of accelerated gear wear, shortened life of the reducer, and low overall efficiency, and optimize the bearing structure , optimize the force condition, optimize the effect of the bearing span
- Summary
- Abstract
- Description
- Claims
- Application Information
AI Technical Summary
Problems solved by technology
Method used
Image
Examples
Embodiment 1
[0026] Such as figure 1 , figure 2 with image 3 As shown, the present invention provides a bearing structure for permanent magnet synchronous direct drive motors in the stirring industry. The bearing structure includes a shaft end bearing and a tail bearing. The shaft end bearing is arranged at one end of the motor shaft extension, and the tail The bearing is located at the tail of the motor.
[0027] The shaft extension end bearing includes a set of cylindrical roller bearing 1 and two sets of cylindrical roller thrust bearings 2. The cylindrical roller bearing 1 and cylindrical roller thrust bearing 2 are arranged in sequence along the motor shaft extension end to the motor tail. An adjustment spring 3 is provided between the two sets of cylindrical roller thrust bearings 2, and the two sets of cylindrical roller thrust bearings 2 are arranged symmetrically relative to the adjustment spring 3; the adjustment springs.
[0028] The tail bearing includes a set of self-alig...
Embodiment 2
[0032] Such as figure 1 , figure 2 with Figure 4 As shown, the present invention provides a bearing structure for permanent magnet synchronous direct drive motors in the stirring industry. The bearing structure includes a shaft end bearing and a tail bearing. The shaft end bearing is arranged at one end of the motor shaft extension, and the tail The bearing is located at the tail of the motor.
[0033] The shaft extension end bearing includes a set of cylindrical roller bearing 1 and two sets of cylindrical roller thrust bearings 2. The cylindrical roller bearing 1 and cylindrical roller thrust bearing 2 are arranged in sequence along the motor shaft extension end to the motor tail. An adjustment spring 3 is provided between the two sets of cylindrical roller thrust bearings 2, and the two sets of cylindrical roller thrust bearings 2 are arranged symmetrically relative to the adjustment spring 3; the adjustment springs.
[0034] The tail bearing includes a set of self-ali...
Embodiment 3
[0038] Such as figure 1 , figure 2 with Figure 5 As shown, the present invention provides a bearing structure for permanent magnet synchronous direct drive motors in the stirring industry. The bearing structure includes a shaft end bearing and a tail bearing. The shaft end bearing is arranged at one end of the motor shaft extension, and the tail The bearing is located at the tail of the motor.
[0039] The shaft extension end bearing includes a set of cylindrical roller bearing 1 and two sets of cylindrical roller thrust bearings 2. The cylindrical roller bearing 1 and cylindrical roller thrust bearing 2 are arranged in sequence along the motor shaft extension end to the motor tail. An adjustment spring 3 is provided between the two sets of cylindrical roller thrust bearings 2, and the two sets of cylindrical roller thrust bearings 2 are arranged symmetrically relative to the adjustment spring 3; the adjustment springs.
[0040] The tail bearing includes a set of self-ali...
PUM
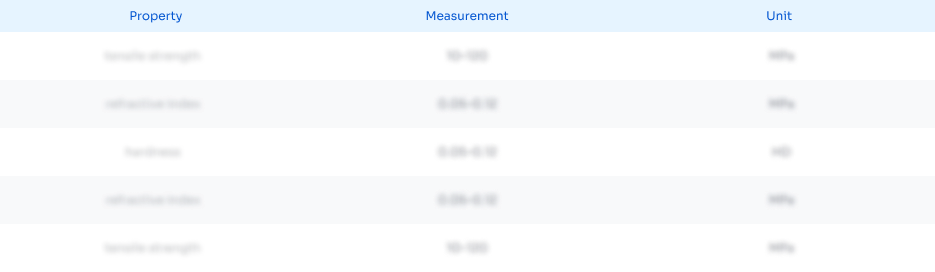
Abstract
Description
Claims
Application Information

- R&D
- Intellectual Property
- Life Sciences
- Materials
- Tech Scout
- Unparalleled Data Quality
- Higher Quality Content
- 60% Fewer Hallucinations
Browse by: Latest US Patents, China's latest patents, Technical Efficacy Thesaurus, Application Domain, Technology Topic, Popular Technical Reports.
© 2025 PatSnap. All rights reserved.Legal|Privacy policy|Modern Slavery Act Transparency Statement|Sitemap|About US| Contact US: help@patsnap.com