Creep constitutive model parameter identification method for creep test
A constitutive model and parameter identification technology, applied in electrical digital data processing, special data processing applications, instruments, etc., can solve the problem of difficult to accurately predict the creep behavior of materials
- Summary
- Abstract
- Description
- Claims
- Application Information
AI Technical Summary
Problems solved by technology
Method used
Image
Examples
Embodiment 1
[0046] A creep constitutive model parameter identification method for creep tests, comprising the following steps:
[0047]S1: In the creep test of the sample material based on the variable cross-section specimen, the variable cross-section specimen is subjected to the creep load F. The selected sample is a plate-shaped sample with a set thickness. The three adjacent and perpendicular surfaces in the plate-shaped sample are the sample analysis surface, the longitudinal section in the thickness direction, and the creep load F acting surface. The analysis surface of the sample is parallel to the direction of the creep load F acting on the sample, and the direction of the creep load F is set as the y direction. Such as Figure 1-2 As shown, the sample material is carbon-manganese steel SA-210C, the sample thickness H is 1 mm, the width W of the sample at the creep load F loading end is 20 mm, and the sample length L is 100 mm. The sample analysis surface is the surface determin...
Embodiment 2
[0075] Under the same environment of embodiment 1, the creep load F2 along the y direction is applied to carbon-manganese steel SA-210C, and the force of F2 is different from the creep load F in embodiment 1, and the same 1600 in embodiment 1 are measured respectively test point at t k =50, 100, 150, 200, 250, 300, 350, 400, 450, 500h, and the finally obtained measurement value conforms to formula (13).
PUM
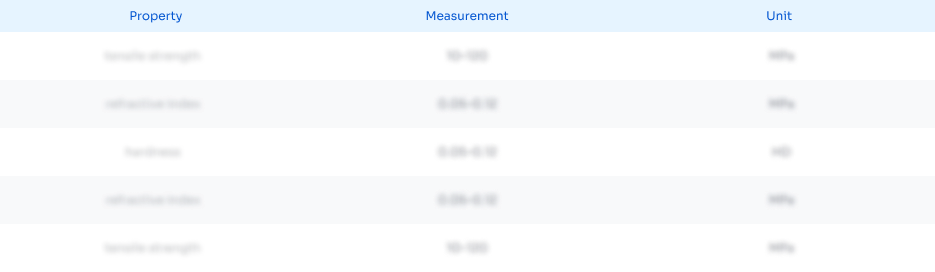
Abstract
Description
Claims
Application Information

- Generate Ideas
- Intellectual Property
- Life Sciences
- Materials
- Tech Scout
- Unparalleled Data Quality
- Higher Quality Content
- 60% Fewer Hallucinations
Browse by: Latest US Patents, China's latest patents, Technical Efficacy Thesaurus, Application Domain, Technology Topic, Popular Technical Reports.
© 2025 PatSnap. All rights reserved.Legal|Privacy policy|Modern Slavery Act Transparency Statement|Sitemap|About US| Contact US: help@patsnap.com