A kind of oil-resistant and high-temperature-resistant modified polyvinyl chloride composite material and preparation method thereof
A polyvinyl chloride and composite material technology, applied in the field of cable materials, can solve the problems of complex preparation process, short service life, high temperature resistance, etc., and achieve the effects of simple process, improved oil resistance and heat resistance, and low production cost
- Summary
- Abstract
- Description
- Claims
- Application Information
AI Technical Summary
Problems solved by technology
Method used
Image
Examples
Embodiment 1
[0033] A preparation method of an oil-resistant and high-temperature-resistant modified polyvinyl chloride composite material, comprising the steps of:
[0034] Masterbatch preparation stage: first weigh 30gPVC and 20gBN, make the weighed sample into a masterbatch of BN / PVC (mass ratio 4:6), fully mix the two components with 500mL tetrahydrofuran, and put the mixed mixture in Ultrasonic in an ultrasonic cleaner for 5-7 hours, so that the two components in the mixture are fully mixed and evenly mixed.
[0035] 2) Masterbatch molding stage: After the ultrasonic wave is completed, use a Buchner funnel to carry out suction filtration, and the masterbatch after suction filtration is naturally air-dried under ventilated conditions, then crushed, and placed in an oven at 50-60°C for 24 hours.
[0036] 3) Take the masterbatch after drying, and gradually add PVC, PA and organotin therein, the specific proportion is PVC:BN:PA:organotin=81:10:5:4, obtain the sample, after mixing evenly, ...
Embodiment 2
[0038] A preparation method of an oil-resistant and high-temperature-resistant modified polyvinyl chloride composite material, comprising the steps of:
[0039] Masterbatch preparation stage: first weigh 30gPVC and 20gBN, make the weighed sample into a masterbatch of BN / PVC (mass ratio 4:6), fully mix the two components with 500mL tetrahydrofuran, and put the mixed mixture in Ultrasonic in an ultrasonic cleaner for 5-7 hours, so that the two components in the mixture are fully mixed and evenly mixed.
[0040] 2) Masterbatch molding stage: After the ultrasonic wave is completed, use a Buchner funnel to carry out suction filtration, and the masterbatch after suction filtration is naturally air-dried under ventilated conditions, then crushed, and placed in an oven at 50-60°C for 24 hours.
[0041] 3) Take the masterbatch after drying, and gradually add PVC, PA and organotin to it, the specific proportion is PVC:BN:PA:organotin=71:10:15:4, obtain the sample, weigh according to the...
Embodiment 3
[0043] A preparation method of an oil-resistant and high-temperature-resistant modified polyvinyl chloride composite material, comprising the steps of:
[0044] 1) Masterbatch preparation stage: first weigh 30gPVC and 20gBN, make the masterbatch of BN / PVC (mass ratio 4:6) from the weighed sample, fully mix the two components with 500mL tetrahydrofuran, and mix the mixture Put it in an ultrasonic cleaner for 5-7 hours, so that the two components in the mixture are fully mixed and evenly mixed.
[0045]2) Masterbatch molding stage: After the ultrasonic wave is completed, use a Buchner funnel to carry out suction filtration. The masterbatch after suction filtration is naturally air-dried under ventilated conditions, then crushed, and placed in an oven at 50-60°C for 24 hours.
[0046] 3) Take the masterbatch after drying, and gradually add PVC, PA and organotin therein, the specific proportion is PVC:BN:PA:organotin=61:10:25:4, obtain the sample, after mixing evenly, Knead at 17...
PUM
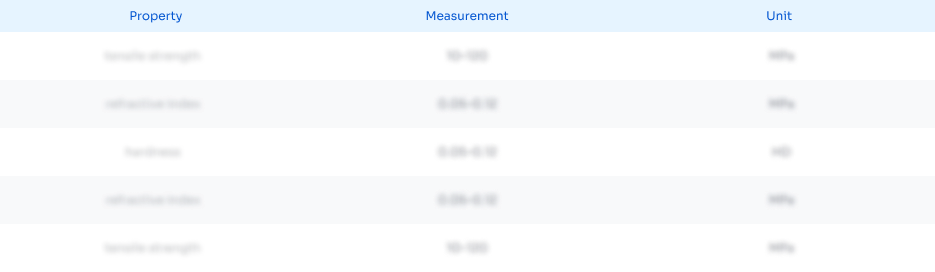
Abstract
Description
Claims
Application Information

- Generate Ideas
- Intellectual Property
- Life Sciences
- Materials
- Tech Scout
- Unparalleled Data Quality
- Higher Quality Content
- 60% Fewer Hallucinations
Browse by: Latest US Patents, China's latest patents, Technical Efficacy Thesaurus, Application Domain, Technology Topic, Popular Technical Reports.
© 2025 PatSnap. All rights reserved.Legal|Privacy policy|Modern Slavery Act Transparency Statement|Sitemap|About US| Contact US: help@patsnap.com