Polyurethane integral skin foam and preparation method thereof
A self-skinning and polyurethane technology, applied in the field of polymer materials, can solve the problems of increasing the density of polyurethane foam, strong odor, thin crust layer, etc., and achieve the effects of good impact resistance, low odor and low volatilization
- Summary
- Abstract
- Description
- Claims
- Application Information
AI Technical Summary
Problems solved by technology
Method used
Image
Examples
Embodiment 1
[0026] Weigh the following raw materials for subsequent use:
[0027] Material A: polyether polyol 70kg, cell opener 0.5kg, foam stabilizer 0.5kg, silicone surfactant 1kg, A-1 1kg, PC-77 catalyst 1kg, diethylene glycol amine 1kg, ethylene glycol 2kg, A33 is 1kg, water 0.5kg.
[0028] Material B: Modified MDI 32kg.
[0029] Put polyether polyol, cell opening agent, foam stabilizer, silicone surfactant, A~1, PC~77 catalyst, diethylene glycol amine, ethylene glycol, A33, water into the reaction kettle in sequence, at room temperature Under the conditions, the rotation speed is 50 rpm, and the mixture A is obtained by stirring for 0.5 h; another modified MDI is used as the B material, and the A and B materials are injected into the closed mold, and after 45 minutes of demoulding, the skinned polyurethane foam product is obtained.
Embodiment 2
[0031] Weigh the following raw materials for subsequent use:
[0032] Material A: polyether polyol 72kg, cell opening agent 1kg, foam stabilizer 0.8kg, silicone surfactant 2kg, A-12kg, PC-77 2kg, diethylene glycol amine 1.5kg, ethylene glycol 4kg, A33 2kg, water 0.8kg.
[0033] Material B: Modified MDI 40kg.
[0034] Put polyether polyol, cell opening agent, foam stabilizer, silicone surfactant, A~1, PC~77 catalyst, diethylene glycol amine, ethylene glycol, A33, water into the reaction kettle in sequence, at room temperature Under the conditions, the rotation speed is 60 rpm, and the mixture A is obtained by stirring for 0.5 h; another modified MDI is taken as the B material, and the mass ratio of the A and B materials is injected into the closed mold, and after 60 seconds of demoulding, the skinned polyurethane foam is obtained. products.
Embodiment 3
[0036] Weigh the following raw materials for subsequent use:
[0037] Material A: polyether polyol 75kg, cell opening agent 1.2kg, foam stabilizer 1kg, silicone surfactant 3kg, A-13kg, PC-77 3kg, diethylene glycol amine 2kg, ethylene glycol 5kg, A33 3kg , water 1kg.
[0038] Material B: Modified MDI 49kg.
[0039] Put polyether polyol, cell opening agent, foam stabilizer, silicone surfactant, A~1, PC~77 catalyst, diethylene glycol amine, ethylene glycol, A33, water into the reaction kettle in sequence, at room temperature Under the conditions, the rotation speed is 65 rpm, and the mixture A is obtained by stirring for 1 h; another modified MDI is used as the B material, and the A and B materials are injected in a closed mold, and after 70 seconds of demoulding, the skinned polyurethane foam product is obtained.
PUM
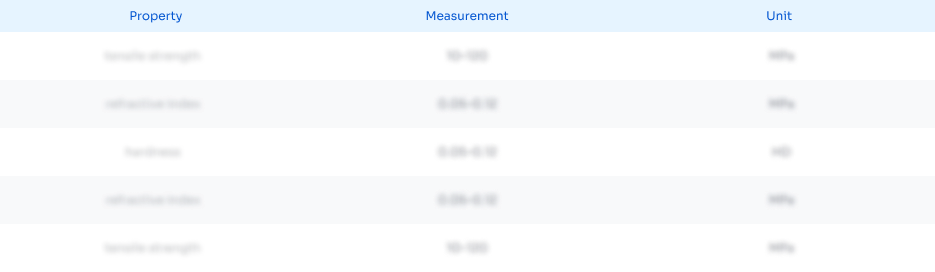
Abstract
Description
Claims
Application Information

- Generate Ideas
- Intellectual Property
- Life Sciences
- Materials
- Tech Scout
- Unparalleled Data Quality
- Higher Quality Content
- 60% Fewer Hallucinations
Browse by: Latest US Patents, China's latest patents, Technical Efficacy Thesaurus, Application Domain, Technology Topic, Popular Technical Reports.
© 2025 PatSnap. All rights reserved.Legal|Privacy policy|Modern Slavery Act Transparency Statement|Sitemap|About US| Contact US: help@patsnap.com