Preparation method of wear-resistant steel block for insert
A technology of wear-resistant steel and inserts, applied in the field of preparation of wear-resistant steel blocks, can solve the problems of inaccurate positioning and easy falling off.
- Summary
- Abstract
- Description
- Claims
- Application Information
AI Technical Summary
Problems solved by technology
Method used
Image
Examples
Embodiment 1
[0030] A preparation method of a wear-resistant steel block capable of precise positioning and anti-falling off is as follows:
[0031] a. Wear-resistant steel block material: 38CrSi, the mass percentage of its composition is: C: 0.35%-0.43%; Si: 1.00%-1.30%; Mn: 0.30%-0.60%; Cr: 1.30%-1.60%.
[0032] b. Wear-resistant steel block structure: The wear-resistant steel block is mainly for the main body 1 and the positioning part 2. The body part 1 and the positioning part 2 are self-contained, and the length and width directions of the body part 1 are designed to be chamfered, which can prevent falling off after casting; at the same time, the sharp corners of the body part 1 are designed to be rounded , to prevent stress concentration during the subsequent casting process; specifically, refer to figure 1 , figure 2 and image 3 As shown, the body portion 1 includes a square upper end surface and a square lower end surface, the lower end surface is larger than the upper end su...
Embodiment 2
[0039] A wear-resistant steel block 2 capable of precise positioning and anti-falling off, the preparation method is as follows:
[0040] a. Wear-resistant steel block material: 38CrSi, the mass percentage of its composition is: C: 0.35%-0.43%; Si: 1.00%-1.30%; Mn: 0.30%-0.60%; Cr: 1.30%-1.60%.
[0041] b. Wear-resistant steel block structure: refer to Example 1.
[0042] c. Die forging forming of wear-resistant steel block: the forging temperature of wear-resistant steel block 38CrSi bar is 1100°C, the holding time is 0.5min / mm, and the initial blank of wear-resistant steel block is formed by one-time die forging, and finally the edge is trimmed by cutting die. A wear-resistant steel block blank is obtained.
[0043] d. Machining of wear-resistant steel block: In order to achieve better precise positioning, the center of the main body part is used as the processing reference, and the positioning part is finished to achieve concentricity or coaxiality between the main body an...
Embodiment 3
[0048] A wear-resistant steel block 3 capable of precise positioning and anti-falling off, the preparation method of which is as follows:
[0049] a. Wear-resistant steel block material: 38CrSi, the mass percentage of its composition is: C: 0.35%-0.43%; Si: 1.00%-1.30%; Mn: 0.30%-0.60%; Cr: 1.30%-1.60%.
[0050] b. Wear-resistant steel block structure: refer to Example 1.
[0051] c. Die forging forming of wear-resistant steel block: the forging temperature of wear-resistant steel block 38CrSi bar is 1150°C, the holding time is 0.6min / mm, and the initial blank of wear-resistant steel block is formed by one-time die forging, and finally the edge is trimmed by cutting die. A wear-resistant steel block blank is obtained.
[0052] d. Machining of wear-resistant steel block: In order to achieve better precise positioning, the center of the main body part is used as the processing reference, and the positioning part is finished to achieve concentricity or coaxiality between the mai...
PUM
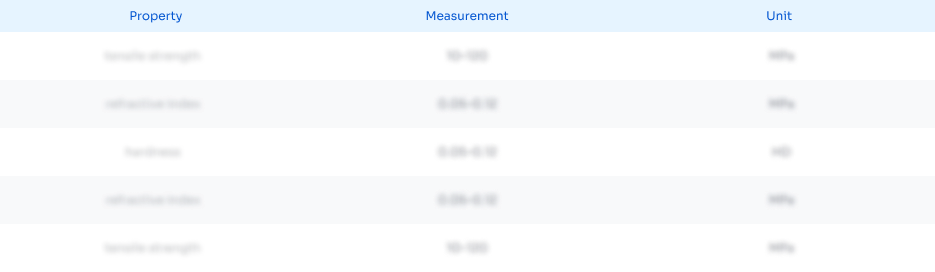
Abstract
Description
Claims
Application Information

- Generate Ideas
- Intellectual Property
- Life Sciences
- Materials
- Tech Scout
- Unparalleled Data Quality
- Higher Quality Content
- 60% Fewer Hallucinations
Browse by: Latest US Patents, China's latest patents, Technical Efficacy Thesaurus, Application Domain, Technology Topic, Popular Technical Reports.
© 2025 PatSnap. All rights reserved.Legal|Privacy policy|Modern Slavery Act Transparency Statement|Sitemap|About US| Contact US: help@patsnap.com