Dry casing insulator vacuum gas pouring system and pouring method thereof
A pouring system and dry bushing technology, applied in the field of power equipment, can solve the problems of air being difficult to be effectively controlled, affecting the electrical performance of the product, restricting the use of the product, etc., achieving high product yield, high mechanical strength, and reducing partial discharge. the effect of the possibility
- Summary
- Abstract
- Description
- Claims
- Application Information
AI Technical Summary
Problems solved by technology
Method used
Image
Examples
Embodiment Construction
[0032] The present invention will be described in detail below in conjunction with the accompanying drawings and specific embodiments.
[0033] figure 1 A dry-type bushing insulator vacuum gas filling casting system is shown, including an epoxy resin casting mold 1, a material injection tank 2, a gas storage pressure tank 3, a gas compressor 4, a vacuum pump 5, an insulating gas storage and inflation device 6 and Gas recovery device 7; the bottom of the injection tank 2 is connected below the epoxy resin casting mold 1 through the injection pipe 21, and the gas storage pressure tank 3 is located between the injection tank 2 and the gas compressor 4, which It is connected to the top of the injection tank 2 and the gas compressor 4; the vacuum pump 5 and the insulating gas storage and inflation device 6 are respectively connected to the epoxy resin pouring through the vacuum pipeline 51 and the gas filling pipeline 61. On the top of the mold 1 , the gas recovery device 7 is con...
PUM
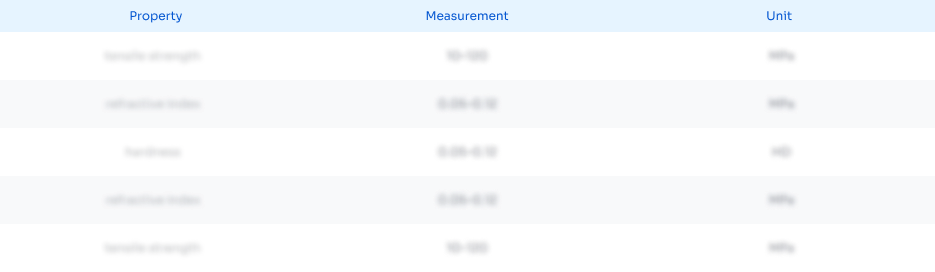
Abstract
Description
Claims
Application Information

- R&D Engineer
- R&D Manager
- IP Professional
- Industry Leading Data Capabilities
- Powerful AI technology
- Patent DNA Extraction
Browse by: Latest US Patents, China's latest patents, Technical Efficacy Thesaurus, Application Domain, Technology Topic, Popular Technical Reports.
© 2024 PatSnap. All rights reserved.Legal|Privacy policy|Modern Slavery Act Transparency Statement|Sitemap|About US| Contact US: help@patsnap.com