Fine boring machining method of large motor seat
A processing method and machine base technology, which are used in metal processing equipment, manufacturing tools, boring/drilling, etc., can solve the problems of difficult clamping, poor positioning accuracy of spigot tires, inaccurate positioning accuracy, etc., and improve the size Accuracy and roughness accuracy, ensuring runout requirements, and improving production efficiency
- Summary
- Abstract
- Description
- Claims
- Application Information
AI Technical Summary
Problems solved by technology
Method used
Examples
Embodiment Construction
[0010] The fine boring processing method of the large motor support of the present invention comprises the following steps:
[0011] The first step is to use a high-precision positioning tire on the boring machine to locate the foot plane and the foot hole, use a dial indicator to punch the end faces of the two ends of the machine base, the first seam, the second seam, and the beating of the iron core. Position the positioning tire and adjust the fine-tuning screw to align the machine base to ensure that the first seam, the second seam, and the iron core have enough processing capacity, then fix the positioning tire on the boring machine table, and press the foot plate of the machine base with a pressure plate place, press the base tightly;
[0012] The second step is to use the special turning tool for the boring machine to turn the end surface of the first seam, the first seam and the iron core to the size required by the product drawing, and re-clamp the turning tool to tur...
PUM
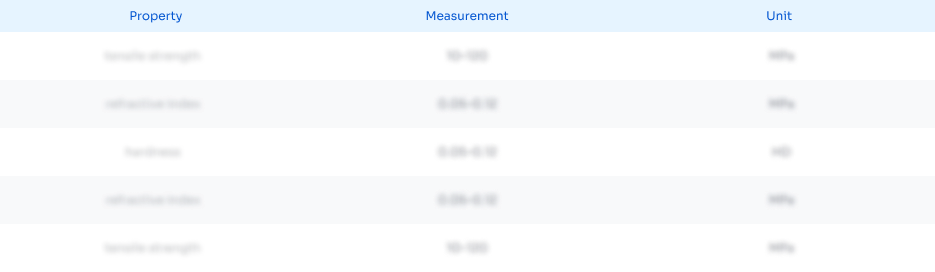
Abstract
Description
Claims
Application Information

- R&D
- Intellectual Property
- Life Sciences
- Materials
- Tech Scout
- Unparalleled Data Quality
- Higher Quality Content
- 60% Fewer Hallucinations
Browse by: Latest US Patents, China's latest patents, Technical Efficacy Thesaurus, Application Domain, Technology Topic, Popular Technical Reports.
© 2025 PatSnap. All rights reserved.Legal|Privacy policy|Modern Slavery Act Transparency Statement|Sitemap|About US| Contact US: help@patsnap.com