Reciprocating twisting and upsetting isometric angle forming method for preparing ultra-fine grain material
An ultra-fine grain, equal-diameter technology, applied in the field of material processing, can solve the problems of weak grain refinement effect of multi-directional forging process, difficult to meet high-performance fine-grain materials, and eccentric load of equal-diameter extrusion process, etc. Achieve the effect of preventing the occurrence or expansion of cracks, enhancing plasticity, and large deformation
- Summary
- Abstract
- Description
- Claims
- Application Information
AI Technical Summary
Problems solved by technology
Method used
Image
Examples
Embodiment Construction
[0028] See figure 1 , figure 2 with image 3 In this embodiment, the reciprocating extrusion twisting equal channel forming method for preparing ultra-fine crystal materials is based on a multi-station forming hydraulic press, and the mold adopts a combined die with upper and lower split molds. figure 1 The lower mold 8 is shown, and the upper sliding block in the multi-station forming hydraulic press provides the clamping force required by the combined die.
[0029] The cavity of the combined die is composed of the left extrusion channel 4, the torsion channel 5, the right extrusion channel 6 and the equal channel angular extrusion channel 9 connected in sequence, and is formed by the inlet end of the left extrusion channel The left hydraulic cylinder 1 and the right hydraulic cylinder 12 at the entrance end of the equal channel angular extrusion channel alternately provide extrusion force and back pressure. The right hydraulic cylinder 12 is placed on the arc slide rail 13 to ad...
PUM
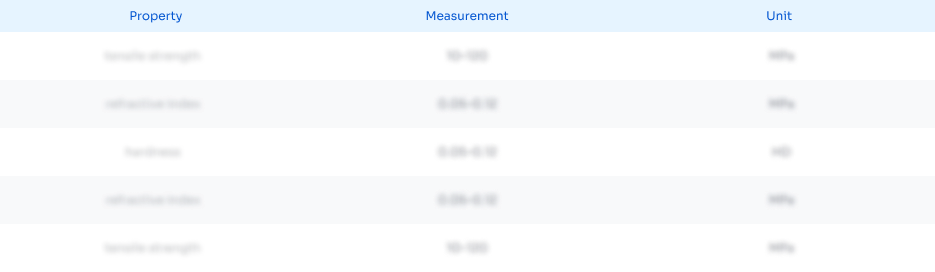
Abstract
Description
Claims
Application Information

- Generate Ideas
- Intellectual Property
- Life Sciences
- Materials
- Tech Scout
- Unparalleled Data Quality
- Higher Quality Content
- 60% Fewer Hallucinations
Browse by: Latest US Patents, China's latest patents, Technical Efficacy Thesaurus, Application Domain, Technology Topic, Popular Technical Reports.
© 2025 PatSnap. All rights reserved.Legal|Privacy policy|Modern Slavery Act Transparency Statement|Sitemap|About US| Contact US: help@patsnap.com