Electrically heating shaft kiln and production process for light-burned magnesia based thereon
A technology of light-burned magnesia and electric heating, which is applied in the production process of light-burned magnesia and the field of electric heating shaft kiln, which can solve problems such as pollution, achieve uniform temperature, reduce heat loss, and evenly heat
- Summary
- Abstract
- Description
- Claims
- Application Information
AI Technical Summary
Problems solved by technology
Method used
Image
Examples
Embodiment Construction
[0024] The specific embodiment of the present invention will be further described below in conjunction with accompanying drawing:
[0025] Such as figure 1 As shown, the electric heating shaft kiln of the present invention comprises a shaft kiln 1, and the shaft kiln 1 is divided into a preheating zone, a calcining zone 6, and a cooling zone from top to bottom; the top of the shaft kiln 1 is provided with a hopper 2 and a Exhaust device 3, water-cooled discharge device 5 is installed at the bottom discharge port 4; electric heating elements 7 are evenly arranged in the kiln wall of the calcining belt 6 along the circumferential direction and the height direction, and the electric heating elements 7 on the same cross section are connected in series After forming a group of heating units, such as figure 2 , image 3 As shown, the electric heating elements 7 in the adjacent heating units along the height direction are staggered, and the electric heating elements 7 of the same ...
PUM
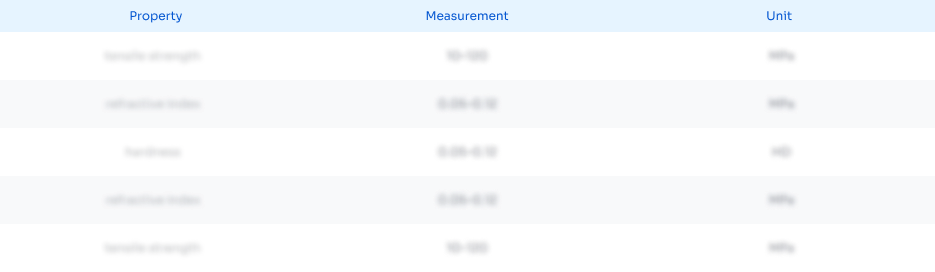
Abstract
Description
Claims
Application Information

- R&D
- Intellectual Property
- Life Sciences
- Materials
- Tech Scout
- Unparalleled Data Quality
- Higher Quality Content
- 60% Fewer Hallucinations
Browse by: Latest US Patents, China's latest patents, Technical Efficacy Thesaurus, Application Domain, Technology Topic, Popular Technical Reports.
© 2025 PatSnap. All rights reserved.Legal|Privacy policy|Modern Slavery Act Transparency Statement|Sitemap|About US| Contact US: help@patsnap.com