Machining technology for submerged-arc welding straight seam steel pipe of shock absorption structure
A shock absorption and processing technology, applied in the field of straight seam submerged arc welded steel pipes, can solve the problems of comparable shock resistance of the weld, and achieve the effects of avoiding pollution, uniform size distribution, and reducing aperture
- Summary
- Abstract
- Description
- Claims
- Application Information
AI Technical Summary
Problems solved by technology
Method used
Image
Examples
Embodiment 1
[0020] (1) Processing of submerged arc welded straight seam steel pipe: carbon steel plate is selected as the base layer and metal steel plate is used as the cladding layer, and the bimetallic composite steel plate is made by hot rolling process, and is milled, pre-bent, JCO formed, and seamed Pre-welding, submerged arc internal welding base carbon steel plate, submerged arc external welding cladding metal plate, ultrasonic inspection, X-ray inspection, finishing treatment, that is, submerged arc welded straight seam steel pipe;
[0021] (2) Processing of shock-absorbing materials: Heat 40kg magnesium ingot to 645-650°C and keep it warm. When the melting rate of magnesium reaches 50%, use a permanent magnetic stirrer to start stirring. After the magnesium ingot is completely melted, add 25kg of aluminum ingot and continue heating to 660°C. -665°C heat preservation and stirring, after the aluminum ingot is completely melted, add 5kg calcined kaolin, 5kg molecular sieve activatio...
Embodiment 2
[0024] (1) Processing of submerged arc welded straight seam steel pipe: carbon steel plate is selected as the base layer and metal steel plate is used as the cladding layer, and the bimetallic composite steel plate is made by hot rolling process, and is milled, pre-bent, JCO formed, and seamed Pre-welding, submerged arc internal welding base carbon steel plate, submerged arc external welding cladding metal plate, ultrasonic inspection, X-ray inspection, finishing treatment, that is, submerged arc welded straight seam steel pipe;
[0025] (2) Processing of shock-absorbing materials: Heat 40kg magnesium ingot to 645-650°C and keep it warm. When the melting rate of magnesium reaches 50%, use a permanent magnetic stirrer to start stirring. After the magnesium ingot is completely melted, add 25kg of aluminum ingot and continue heating to 660°C. -665°C heat preservation and stirring, after the aluminum ingot is completely melted, add 5kg calcined kaolin, 5kg molecular sieve activatio...
Embodiment 3
[0028] (1) Processing of submerged arc welded straight seam steel pipe: carbon steel plate is selected as the base layer and metal steel plate is used as the cladding layer, and the bimetallic composite steel plate is made by hot rolling process, and is milled, pre-bent, JCO formed, and seamed Pre-welding, submerged arc internal welding base carbon steel plate, submerged arc external welding cladding metal plate, ultrasonic inspection, X-ray inspection, finishing treatment, that is, submerged arc welded straight seam steel pipe;
[0029] (2) Processing of shock-absorbing materials: Heat 40kg magnesium ingot to 645-650°C and keep it warm. When the melting rate of magnesium reaches 50%, use a permanent magnetic stirrer to start stirring. After the magnesium ingot is completely melted, add 25kg of aluminum ingot and continue heating to 660°C. -665°C heat preservation and stirring, after the aluminum ingot is completely melted, add 5kg calcined kaolin, 5kg molecular sieve activatio...
PUM
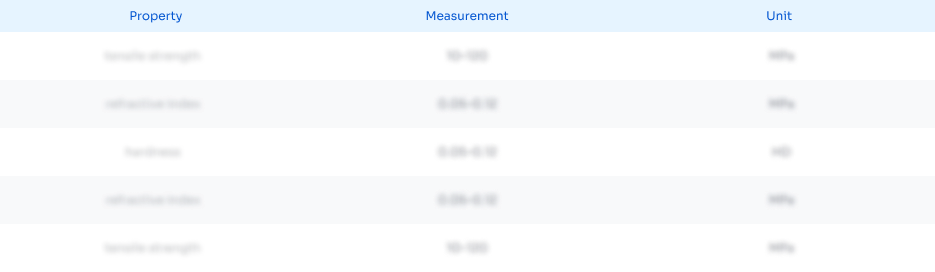
Abstract
Description
Claims
Application Information

- R&D Engineer
- R&D Manager
- IP Professional
- Industry Leading Data Capabilities
- Powerful AI technology
- Patent DNA Extraction
Browse by: Latest US Patents, China's latest patents, Technical Efficacy Thesaurus, Application Domain, Technology Topic, Popular Technical Reports.
© 2024 PatSnap. All rights reserved.Legal|Privacy policy|Modern Slavery Act Transparency Statement|Sitemap|About US| Contact US: help@patsnap.com