Vehicle cab frame structure optimization method
A frame structure and optimization method technology, applied in design optimization/simulation, special data processing applications, instruments, etc., can solve problems such as large blindness and incomplete optimization, achieve strong pertinence, overcome blindness, and drive The effect of room and frame structure optimization
- Summary
- Abstract
- Description
- Claims
- Application Information
AI Technical Summary
Problems solved by technology
Method used
Image
Examples
Embodiment 1
[0040] The vehicle cab frame structure optimization method of the present embodiment comprises the following steps:
[0041] A. Construct the vibration transmission path analysis model for the cab-frame structure entity to be optimized. Taking the driver's seat as the response point, construct the vibration transmission path analysis model of the total system, the vibration transmission path analysis model of the frame subsystem and the cab sub-system respectively. The system vibration transfer path analysis model is tested to obtain the transfer function and working condition data of the total system and two subsystems, analyze the vibration contribution and frequency response of each transfer path in the total system and two subsystems, and determine the overall system and two subsystems. The vibration paths and key frequencies with large contributions in the two subsystems are used as the optimization target path;
[0042] After the transmission path analysis in this embodi...
PUM
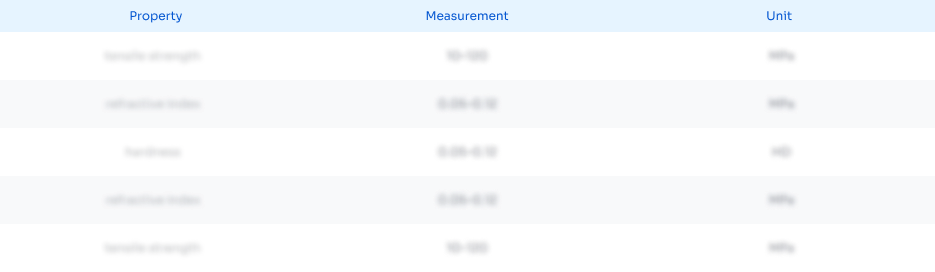
Abstract
Description
Claims
Application Information

- R&D Engineer
- R&D Manager
- IP Professional
- Industry Leading Data Capabilities
- Powerful AI technology
- Patent DNA Extraction
Browse by: Latest US Patents, China's latest patents, Technical Efficacy Thesaurus, Application Domain, Technology Topic, Popular Technical Reports.
© 2024 PatSnap. All rights reserved.Legal|Privacy policy|Modern Slavery Act Transparency Statement|Sitemap|About US| Contact US: help@patsnap.com