Pipefitting for connecting metal compound tubular product
A metal composite pipe and metal insert technology, applied in the direction of pipe/pipe joint/pipe fitting, pipe element, pipe connection arrangement, etc., can solve the problem of leakage at the joint between plastic and metal, prevent air trapping and ensure sealing performance , the effect of low cost
- Summary
- Abstract
- Description
- Claims
- Application Information
AI Technical Summary
Problems solved by technology
Method used
Image
Examples
Embodiment 1
[0047] like Figure 1-2 As shown, the pipe fitting 10 used to connect the metal composite pipe 20 includes a plastic pipe fitting body 1, both ends of the plastic pipe fitting body 1 are socket hot-melt connection ends 11, and the socket hot-melt connection end 11 includes two layers in the radial direction , are respectively the outer layer tube 111 and the inner layer tube 112, the length of the outer layer tube 111 is greater than the length of the inner layer tube 112, the diameter of the outer layer tube 111 is greater than the diameter of the inner layer tube 112,
[0048] A socket 12 is formed between the outer tube 111 and the inner tube 112. The socket 12 includes a first sealing surface 121, a second sealing surface 122 and a third sealing surface 123. The first sealing surface 121 is used for compounding with metal The plastic inner layer 201 of the pipe 20 is hot-melt connected, the second sealing surface 122 is in contact with the metal middle layer 202 of the met...
Embodiment 2
[0065] like Figure 3-4 As shown, the pipe fitting 10 is a right-angle two-way connection, one end of which is a socket hot-melt connection end 11, and the other end is integrally injection-molded with the metal insert 2, and the center of the metal insert 2 is provided with a through hole 13 communicating with the plastic pipe fitting body 1. The threaded hole 21. The socket hot-melt connection end 11 is used for connecting with the metal composite pipe 20, and the end with the metal insert 2 is used for connecting with the faucet.
[0066] like Figure 5 As shown, the cross section of the storage tank 124 is rectangular, including a first axial surface 124a, a second axial surface 124b and a first radial surface 124c, the first axial surface 124a is connected with the second sealing surface 122, the second The two axial surfaces 124b are connected to the third sealing surface 123, and the first radial surface 124c is connected to the first axial surface 124a and the second...
PUM
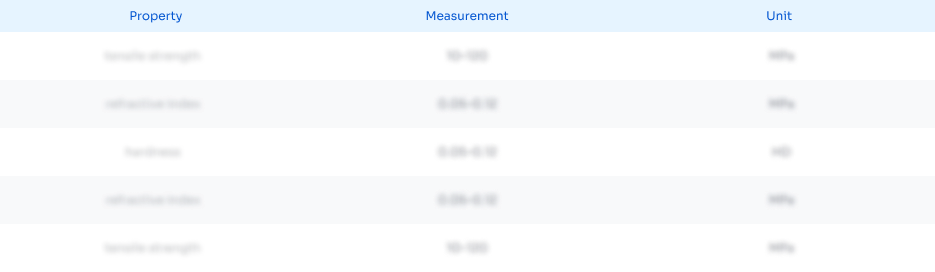
Abstract
Description
Claims
Application Information

- R&D Engineer
- R&D Manager
- IP Professional
- Industry Leading Data Capabilities
- Powerful AI technology
- Patent DNA Extraction
Browse by: Latest US Patents, China's latest patents, Technical Efficacy Thesaurus, Application Domain, Technology Topic, Popular Technical Reports.
© 2024 PatSnap. All rights reserved.Legal|Privacy policy|Modern Slavery Act Transparency Statement|Sitemap|About US| Contact US: help@patsnap.com