Chip sputtering jig and sputtering method
A sputtering and jig technology, applied in the field of chip sputtering jig, can solve the problems of affecting the service life of the chip, the complex sputtering process, affecting the function of the chip, etc., to ensure the service life, save the time of sputtering, and improve the efficiency. Effect
- Summary
- Abstract
- Description
- Claims
- Application Information
AI Technical Summary
Problems solved by technology
Method used
Image
Examples
Embodiment 1
[0034] see figure 1 . The chip sputtering fixture includes an upper backing paper 1, a pyrolytic glue layer 2 and a lower backing paper 3, the pyrolytic glue layer 2 includes an upper surface and a lower surface, and the upper backing paper 1 is arranged on the pyrolytic glue The upper surface of the layer 2, the lower bottom paper 3 is arranged on the lower surface of the pyrolysis adhesive layer 2, and the upper bottom paper 1 and the lower bottom paper 3 are used to protect the pyrolysis adhesive layer 2; Layer 2 is a high-low temperature pyrolytic glue that loses its viscosity at a preset temperature, and the preset temperature of the pyrolytic glue layer 2 is higher than the sputtering temperature, so as to ensure that the pyrolytic glue layer 2 is still Has very good stickiness.
[0035] see figure 2 . The upper surface of the pyrolytic adhesive layer 2 is used to set the chip 5. Since the pyrolytic adhesive layer 2 has good viscosity at normal temperature, the chip...
Embodiment 2
[0042] see Figure 4 . The difference between this embodiment and Embodiment 1 is that the chip sputtering fixture also includes a support layer 4, and the support 4 is arranged between the pyrolytic adhesive layer 2 and the bottom paper 3, that is, the The supporting layer 4 is arranged on the lower surface of the pyrolytic adhesive layer 2 , and the bottom paper 3 is arranged on the side of the supporting layer 4 away from the pyrolytic adhesive layer 2 .
[0043] The support layer 4 includes a high-temperature-resistant Mylar sheet 40 and an adhesive layer 41, wherein the high-temperature-resistant Mylar sheet 40 is arranged on the lower surface of the pyrolytic adhesive layer 2, which has good heat resistance and is used for Supporting and protecting the pyrolytic adhesive layer 2 and the chip 5, the adhesive layer 41 is arranged between the high temperature-resistant Mylar sheet 40 and the lower backing paper 3, and is used to paste the sputtering fixture and the furnace...
PUM
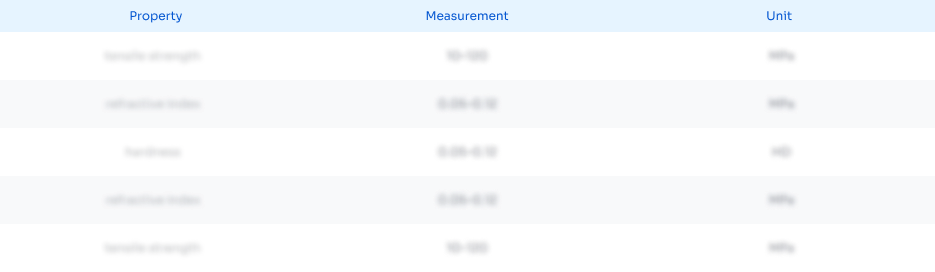
Abstract
Description
Claims
Application Information

- Generate Ideas
- Intellectual Property
- Life Sciences
- Materials
- Tech Scout
- Unparalleled Data Quality
- Higher Quality Content
- 60% Fewer Hallucinations
Browse by: Latest US Patents, China's latest patents, Technical Efficacy Thesaurus, Application Domain, Technology Topic, Popular Technical Reports.
© 2025 PatSnap. All rights reserved.Legal|Privacy policy|Modern Slavery Act Transparency Statement|Sitemap|About US| Contact US: help@patsnap.com