Steel surface spraying process
A surface spraying, steel technology, applied in the direction of metal material coating process, coating, melting spraying, etc., can solve the problems of rust, steel has a short service life, easy to be corroded, etc., to improve the service life, not easy to be damaged , The effect of not easy to oxidize or corrode
- Summary
- Abstract
- Description
- Claims
- Application Information
AI Technical Summary
Problems solved by technology
Method used
Examples
Embodiment Construction
[0016] The following describes the embodiments of the present invention in detail.
[0017] The invention provides a steel surface spraying process, which is characterized in that it comprises the following steps:
[0018] a. To remove impurities and remove impurities on the surface;
[0019] b. Clean and dry, rinse and dry with high-pressure water gun;
[0020] c, spraying an insulating layer, spraying an insulating layer on the surface of the dried steel, the thickness of the insulating layer is 20-30 μm;
[0021] d, spraying an anti-oxidation layer, spraying an anti-oxidation layer on the basis of the insulating layer, the thickness of the anti-oxidation layer is 30-50 μm;
[0022] E, spray corrosion-resistant layer, spray corrosion-resistant layer on the basis of anti-oxidation layer, the thickness of described corrosion-resistant layer is 50-80 μ m;
[0023] f, cooling, vacuum cooling to room temperature.
[0024] The equipment selected for spraying in this embodiment...
PUM
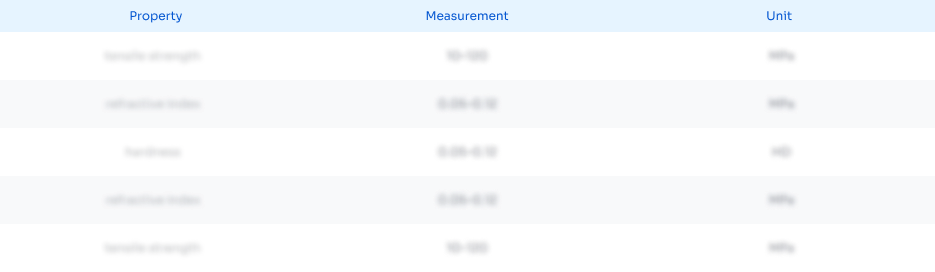
Abstract
Description
Claims
Application Information

- R&D
- Intellectual Property
- Life Sciences
- Materials
- Tech Scout
- Unparalleled Data Quality
- Higher Quality Content
- 60% Fewer Hallucinations
Browse by: Latest US Patents, China's latest patents, Technical Efficacy Thesaurus, Application Domain, Technology Topic, Popular Technical Reports.
© 2025 PatSnap. All rights reserved.Legal|Privacy policy|Modern Slavery Act Transparency Statement|Sitemap|About US| Contact US: help@patsnap.com