Fabricated concrete variable-section end-column-type shear wall member and construction method thereof
A shear wall and variable section technology, which is applied to building components, walls, manufacturing tools, etc., can solve the problem of weak sleeve connections, difficult staggered processing of horizontal steel bar joints, and no steel bars formed in the steel bars of end-column shear wall components. Skeleton etc.
- Summary
- Abstract
- Description
- Claims
- Application Information
AI Technical Summary
Problems solved by technology
Method used
Image
Examples
Embodiment 1
[0058] Such as Figure 1-3 As shown, a prefabricated concrete variable-section end-column shear wall member includes a shear wall body 11 and a terminal column 12, and the end column 12 is directly connected to one side of the shear wall body 11. The end-column shear wall The force wall component is divided into the upper section 1A of the component and the lower section 1B of the component formed by reducing the variable section, which is a whole formed by pouring concrete; the upper section 1A of the component is pre-embedded with vertical steel bars 101, horizontal steel bars 102 and tie bars 103; The outer end of the end column 12 and the shear wall 11 is provided with an edge member 104, and the vertical reinforcement 101 in the edge member 104 is reinforced into a vertical reinforcement 1041 of the edge member, and a stirrup 1042 is installed; Stretch out the top of the end-column shear wall member to the reinforcing bar 101 and the vertical reinforcing bar 1041 of the e...
Embodiment 2
[0060] Such as Figure 4-8 As shown, a manufacturing mold of a fabricated concrete variable-section end-column shear wall member described in Example 1 of the present invention includes a shear wall limb mold 21 and an end-column mold 22, and is characterized in that: Described mold also comprises formwork oblique support 23, buttress 24; Described shear wall limb mold 21 comprises shear wall limb outer template 211, shear wall limb top template 212, wall core surface template 213, shear wall limb variable section Baffle plate 214, shear wall limb bottom formwork 215, shear wall limb column top upper side formwork 216, shear wall limb L-shaped coupling beam support template 217, shear wall limb vertical tunnel mold 218; The column mold 22 includes the inner formwork 221 of the upper section of the end column, the inner formwork 222 of the lower section of the end column, the outer formwork 223 of the upper section of the end column, the outer formwork 224 of the lower section ...
Embodiment 3
[0069] On the basis of Examples 1-2, a construction method of the present invention for making a prefabricated concrete variable-section end-column shear wall member described in Example 1 includes the prefabricated concrete variable-section end-column shear wall member The method of making and installing the force wall components is as follows:
[0070] S01. Formwork support and steel bar erection: such as Figure 4-8 As shown, the control line is played on the flat production platform, and the wall core surface formwork 213 and the column core surface formwork 226 are installed; the vertical steel bars 1041 and stirrups 1042 of the edge components of the edge components 104 are installed and bound firmly; the end columns are installed and bound The vertical steel bar 101 and the horizontal steel bar 102 of the lower layer in the type shear wall component mold, and the vertical steel bar 101, the vertical steel bar 1041 of the edge member and the stirrup bar 1042 are embedded...
PUM
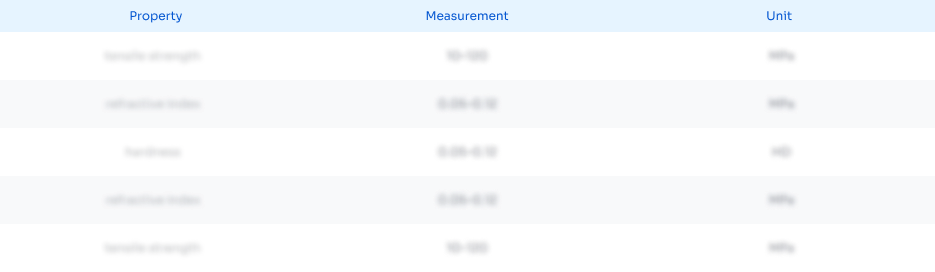
Abstract
Description
Claims
Application Information

- Generate Ideas
- Intellectual Property
- Life Sciences
- Materials
- Tech Scout
- Unparalleled Data Quality
- Higher Quality Content
- 60% Fewer Hallucinations
Browse by: Latest US Patents, China's latest patents, Technical Efficacy Thesaurus, Application Domain, Technology Topic, Popular Technical Reports.
© 2025 PatSnap. All rights reserved.Legal|Privacy policy|Modern Slavery Act Transparency Statement|Sitemap|About US| Contact US: help@patsnap.com