A method for segmenting sintering flue gas and using blast furnace to treat flue gas pollutants
A technology for sintering flue gas and flue gas treatment, which is applied in separation methods, gas treatment, chemical instruments and methods, etc., can solve the problem of high cost of coordinated treatment of sintering flue gas pollutants, achieve high social and ecological value, solve enterprise problems, The effect of reducing governance costs
- Summary
- Abstract
- Description
- Claims
- Application Information
AI Technical Summary
Problems solved by technology
Method used
Image
Examples
Embodiment Construction
[0037] The present invention will be described in further detail below in conjunction with the accompanying drawings and specific embodiments.
[0038] The invention provides a method for segmenting sintering flue gas and using a blast furnace to treat flue gas pollutants, such as figure 1 As shown, the equipment used in this method includes: sintering machine 1, sintering air box 2, direct discharge flue 3, flue to be treated 4, electrostatic precipitator 5, first induced draft fan 6, flue gas treatment device 7, second induced draft fan Fan 8, chimney 9, third induced draft fan 10, oxygen adding device 11, hot blast stove 12, fourth induced draft fan 13, blast furnace 14.
[0039] Sintering machine 1 includes a plurality of sintering bellows 2. Along the running direction of the sintering trolley, the flue gas in the sintering bellows 2 is divided into the flue gas that can be discharged directly and the flue gas to be treated. The flue gas in 2 is low SO 2 , low temperatu...
PUM
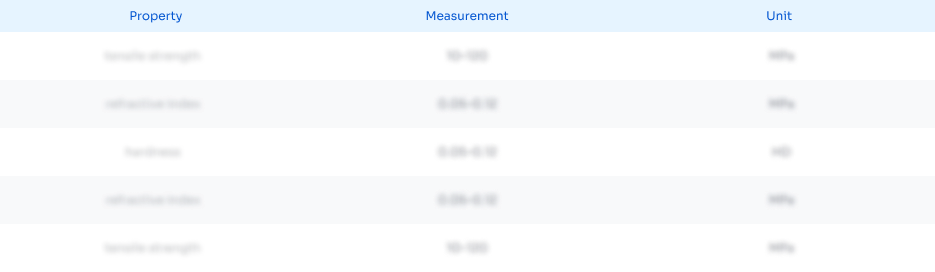
Abstract
Description
Claims
Application Information

- Generate Ideas
- Intellectual Property
- Life Sciences
- Materials
- Tech Scout
- Unparalleled Data Quality
- Higher Quality Content
- 60% Fewer Hallucinations
Browse by: Latest US Patents, China's latest patents, Technical Efficacy Thesaurus, Application Domain, Technology Topic, Popular Technical Reports.
© 2025 PatSnap. All rights reserved.Legal|Privacy policy|Modern Slavery Act Transparency Statement|Sitemap|About US| Contact US: help@patsnap.com