Flexible training device and training method for aircraft annular pneumatic riveting
A riveting and ring-shaped technology, which is used in aerospace components, component assembly and manufacturing, automobiles, machinery, and ships. It can solve the problems of poor quality consistency of ring-shaped multi-nail riveting, unstable riveting quality, and high labor intensity, and achieve stability and efficiency. High efficiency, improved training efficiency, and large spatial freedom
- Summary
- Abstract
- Description
- Claims
- Application Information
AI Technical Summary
Problems solved by technology
Method used
Image
Examples
Embodiment Construction
[0028] The present invention will be described in detail below in conjunction with specific embodiments. The following examples will help those skilled in the art to further understand the present invention, but do not limit the present invention in any form. It should be noted that those skilled in the art can make several modifications and improvements without departing from the concept of the present invention. These all belong to the protection scope of the present invention.
[0029] Such as figure 1 — Figure 4 As shown, the technical solution of the present invention provides a flexible training device for circular pneumatic riveting of aircraft, including a riveting platform 2 and a joint robot 1, and the riveting platform 2 is fixedly connected with the joint robot 1 . The articulated robot 1 can be fixed on an elevator or a workbench / frame, and the lift or workbench / frame can be used to adjust the height of the articulated robot and provide positioning and support...
PUM
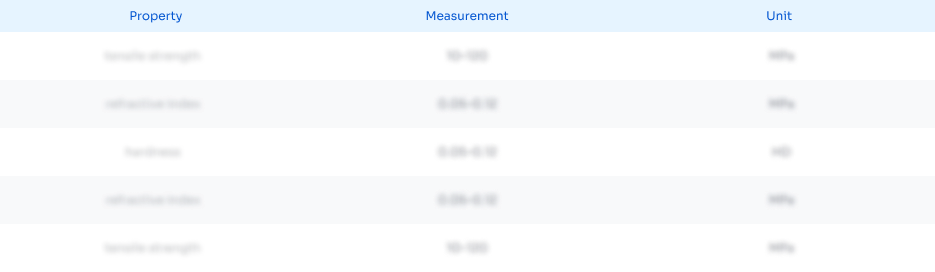
Abstract
Description
Claims
Application Information

- R&D Engineer
- R&D Manager
- IP Professional
- Industry Leading Data Capabilities
- Powerful AI technology
- Patent DNA Extraction
Browse by: Latest US Patents, China's latest patents, Technical Efficacy Thesaurus, Application Domain, Technology Topic, Popular Technical Reports.
© 2024 PatSnap. All rights reserved.Legal|Privacy policy|Modern Slavery Act Transparency Statement|Sitemap|About US| Contact US: help@patsnap.com