Heavy numerical control machine tool thermal error compensation control system based on CPS (Cyber-Physical Systems) and thermal error compensation method
A heavy-duty CNC machine tool, compensation control technology, applied in the general control system, control/adjustment system, computer control, etc., can solve the problems of insufficient network communication capabilities, low intelligence, poor independence, etc., to achieve exquisite design and versatility Strong, easily replaceable effect
- Summary
- Abstract
- Description
- Claims
- Application Information
AI Technical Summary
Problems solved by technology
Method used
Image
Examples
Embodiment Construction
[0048] The present invention will be further described in detail below in conjunction with the accompanying drawings and specific embodiments.
[0049] Such as figure 1 As shown, a CPS-based thermal error compensation control system for heavy-duty CNC machine tools in the present invention includes an embedded acquisition card A, an operation controller B, a CNC connector C and a system power supply.
[0050] The embedded acquisition card A is placed in the electrical cabinet of the CNC machine tool, including the physical layer and network layer in the CPS architecture. The embedded acquisition card A is used to collect the temperature information of the machine tool measuring point and the displacement thermal error of the tool tip of the machine tool spindle, upload the collected data to the cloud server through the wireless network, and send the data to the operation controller B after preprocessing.
[0051] The embedded acquisition card A includes a sensor 1 , a data pr...
PUM
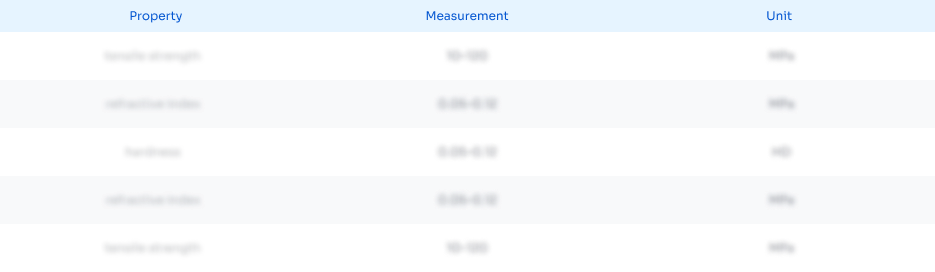
Abstract
Description
Claims
Application Information

- R&D
- Intellectual Property
- Life Sciences
- Materials
- Tech Scout
- Unparalleled Data Quality
- Higher Quality Content
- 60% Fewer Hallucinations
Browse by: Latest US Patents, China's latest patents, Technical Efficacy Thesaurus, Application Domain, Technology Topic, Popular Technical Reports.
© 2025 PatSnap. All rights reserved.Legal|Privacy policy|Modern Slavery Act Transparency Statement|Sitemap|About US| Contact US: help@patsnap.com