Structure used for motor rotor cooling
A technology of motor rotor and rotor coil, which is applied in cooling/ventilation device, magnetic circuit shape/style/structure, electric components, etc. efficiency, improve heat dissipation efficiency, and reduce costs
- Summary
- Abstract
- Description
- Claims
- Application Information
AI Technical Summary
Problems solved by technology
Method used
Image
Examples
Embodiment Construction
[0023] Such as figure 1 As shown, the motor part in the figure includes a motor housing 1, a motor stator 2, a stator winding 3, a motor rotor 14, and a rotating shaft 13; figure 1 It also includes the transmission casing 4, the transmission gear 5 of the transmission part, the liquid oil 9 at the bottom of the transmission casing 4, and the oil pump 6 and the oil pump control unit 16 outside the transmission.
[0024] The transmission gear 5 and the center of the rotating shaft 13 are respectively provided with a gear hollow cavity 12 and a shaft hollow cavity 11 connected to each other, and one end of the transmission gear connected to the rotating shaft is provided with a return hole 15, and the other end of the gear hollow cavity of the transmission gear is connected to Through the oil outlet 7 of the oil pump 6, the oil pump 6 is controlled and connected by the oil pump control signal 17 of the oil pump control unit 16, and the oil 9 inside the transmission is connected t...
PUM
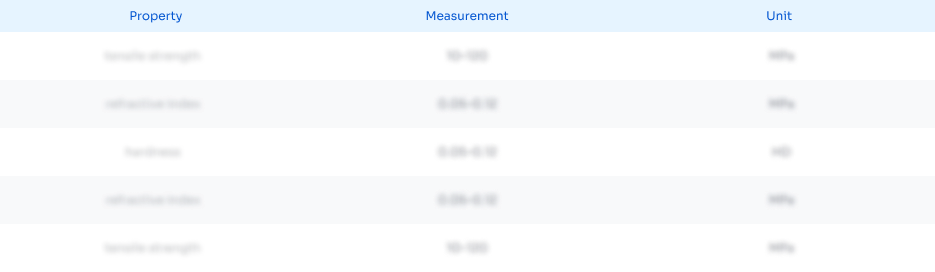
Abstract
Description
Claims
Application Information

- R&D Engineer
- R&D Manager
- IP Professional
- Industry Leading Data Capabilities
- Powerful AI technology
- Patent DNA Extraction
Browse by: Latest US Patents, China's latest patents, Technical Efficacy Thesaurus, Application Domain, Technology Topic, Popular Technical Reports.
© 2024 PatSnap. All rights reserved.Legal|Privacy policy|Modern Slavery Act Transparency Statement|Sitemap|About US| Contact US: help@patsnap.com