Method for optimizing distribution of roll pressure
A technology for optimizing configuration and rolls, applied in tension/pressure control, contour control, etc., can solve problems such as increased production costs, reduced service life of straightening machine rolls, and poor plate shape, so as to increase equipment service life and reduce production Cost, the effect of satisfying operating habits
- Summary
- Abstract
- Description
- Claims
- Application Information
AI Technical Summary
Problems solved by technology
Method used
Examples
Embodiment Construction
[0009] The present invention will be further described below through embodiment.
[0010] A method for optimizing the configuration of roll pressure, the control setting of steel plate hard bending: the steel bite speed is less than or equal to 20-30 rpm, the normal rolling speed is 40-60 rpm, and the set value of roll pressure is less than or equal to 2 -3mm; the steel biting speed is not less than 15-25 rpm, and the minimum roller pressure setting is 0.5-1.5mm. The pressure of the roll is the roll diameter difference.
[0011] In order to make the rolling process stable and meet the operating habits of all steel rolling workers, the optimum value of the roll pressure setting is 1.0-1.5mm. The invention optimizes the pressure configuration of the rolls to reduce the consumption of the rolls, control the hard bending of the steel plate and improve the surface quality of the steel plate to meet the requirements.
[0012] The present invention sets a configuration range of opt...
PUM
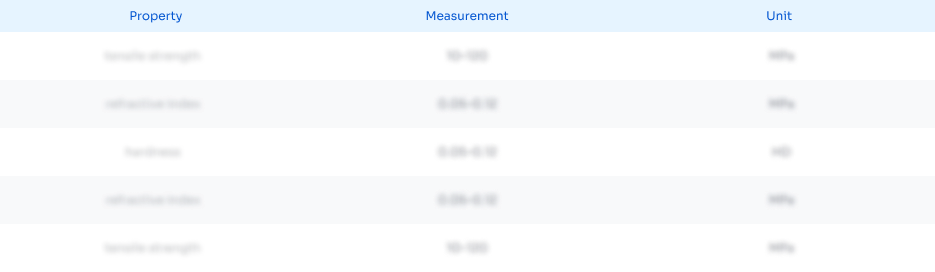
Abstract
Description
Claims
Application Information

- R&D Engineer
- R&D Manager
- IP Professional
- Industry Leading Data Capabilities
- Powerful AI technology
- Patent DNA Extraction
Browse by: Latest US Patents, China's latest patents, Technical Efficacy Thesaurus, Application Domain, Technology Topic, Popular Technical Reports.
© 2024 PatSnap. All rights reserved.Legal|Privacy policy|Modern Slavery Act Transparency Statement|Sitemap|About US| Contact US: help@patsnap.com