Method for preparing low temperature co-fired ceramic substrate cavity structure
A technology of low-temperature co-fired ceramics and substrates, which is applied in semiconductor/solid-state device manufacturing, electrical components, circuits, etc., can solve the problems of increasing the complexity and cost of LTCC substrate preparation processes, achieve easy operation, simple process, and solve pollution problems. cavity effect
- Summary
- Abstract
- Description
- Claims
- Application Information
AI Technical Summary
Problems solved by technology
Method used
Image
Examples
preparation example Construction
[0039] figure 1 It is a schematic flowchart showing a method for preparing a cavity structure of an LTCC substrate 1 according to an embodiment of the present invention. in the figure 1 In the shown embodiment, the method for preparing the cavity structure of the LTCC substrate 1 of the present invention has the following steps: cutting the rolled LTCC green ceramic tape into several pieces of LTCC green ceramic sheets 1A, and then cutting the partially cut pieces The LTCC green ceramic sheets 1A are stacked in the first stage in sequence, thereby forming the upper cover plate 2 and the lower layer plate 4 respectively; in addition, several pieces of LTCC green ceramic sheets 1A that have been cut are punched, and then several pieces of LTCC green ceramic sheets that have been punched are punched. The green ceramic sheet 1A is laminated in the first stage in order to form a sub-layer 3 with a cavity structure; the sub-layer 3 and the lower layer 4 are laminated in the second ...
Embodiment 1)
[0048] According to the preparation method of the cavity structure of the LTCC substrate 1 according to Embodiment 1 of the present invention, the specific steps are as follows:
[0049] First of all, the cut 5 pieces of LTCC green ceramic sheets 1A are sequentially put into the stacker for the first stage of stacking. In the stacking process, the stacking pressure is 5 MPa, the stacking temperature is 65° C., and the stacking time is 120 seconds, thereby making the upper cover plate 2 of the cavity structure of the LTCC substrate 1 . Then the cut 15 pieces of LTCC green ceramic sheets 1A are sequentially put into the stacker for the first stage of stacking, and the lower layer plate 4 of the cavity structure of the LTCC substrate 1 is made.
[0050] Then, 10 LTCC green ceramic sheets 1A were drilled, and according to the design height of the cavity structure, the first stage was carried out on the 10 LTCC green ceramic sheets 1A that had been drilled using the same process co...
Embodiment 2)
[0054] According to the preparation method of the cavity structure of the LTCC substrate 1 according to Embodiment 2 of the present invention, the specific steps are as follows:
[0055] First, put the cut 10 pieces of LTCC green ceramic sheets 1A into the lamination machine in turn for the first stage of lamination. In the lamination process, the lamination pressure is 3 MPa, the lamination temperature is 55° C., and the lamination time is 90 seconds, thus the upper cover plate 2 of the cavity structure of the LTCC substrate 1 is manufactured. Then the cut 15 pieces of LTCC green ceramic sheets 1A are sequentially put into the stacker for the first stage of stacking, and the lower layer plate 4 of the cavity structure of the LTCC substrate 1 is made.
[0056] Then, 10 LTCC green ceramic sheets 1A were drilled, and according to the design height of the cavity structure, the first stage was carried out on the 10 LTCC green ceramic sheets 1A that had been drilled using the same ...
PUM
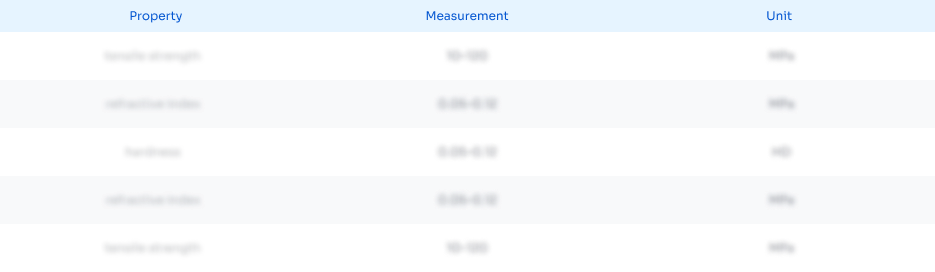
Abstract
Description
Claims
Application Information

- R&D
- Intellectual Property
- Life Sciences
- Materials
- Tech Scout
- Unparalleled Data Quality
- Higher Quality Content
- 60% Fewer Hallucinations
Browse by: Latest US Patents, China's latest patents, Technical Efficacy Thesaurus, Application Domain, Technology Topic, Popular Technical Reports.
© 2025 PatSnap. All rights reserved.Legal|Privacy policy|Modern Slavery Act Transparency Statement|Sitemap|About US| Contact US: help@patsnap.com