Device and method for drilling positioning and normal measurement of robot
A technology of robotic hole making and measuring devices, applied in measuring devices, optical devices, instruments, etc., can solve problems such as scratches, high mechanical failure rate, low reliability, etc., and achieve the effect of low cost and high robustness
- Summary
- Abstract
- Description
- Claims
- Application Information
AI Technical Summary
Problems solved by technology
Method used
Image
Examples
Embodiment 1
[0027] see Figure 1-Figure 3 , which is used for robot hole positioning and normal measurement device, including TOF distance method
[0028] A line measurement sensor module (1), a reflector (2), a reflector drive mechanism (3) and an automatic drilling and riveting machine end actuator (4), characterized in that: the automatic drilling and riveting machine end actuator (4) and The plane to be processed (5) is vertical, and the TOF distance normal measurement sensor module (1) and the mirror driving mechanism (3) are connected through a vertical rigid bracket, and the mirror driving structure (3) is connected to the mirror (2); through total reflection The mirror driving mechanism (3) is used to adjust the reflection angle of the mirror (2) so that the optical path is parallel to the drill feed track of the end actuator (4) of the automatic drilling and riveting machine tool, and then the sensor module (1) is measured by the TOF distance normal The embedded system digitally...
Embodiment 2
[0030] This embodiment is basically the same as Embodiment 1, and the special features are as follows: the TOF distance normal measurement sensor
[0031] The module (1) includes an array photosensitive and light emitting module (1.1), a positioning and normal direction sensor module (1.2), and an embedded system digitally controls the array type photosensitive and emitting module (1.1) and the positioning and normal direction sensor module (1.2 ).
[0032] The array-type photosensitive and light-emitting module (1.1) includes a charge-coupled device, a field programmable gate array, multiple light-emitting diode light sources, and a driving circuit for light-emitting diode light sources; the LED light sources are arranged concentrically, and the array-type photosensitive and light-emitting module (1.1 ) is set at a position where the coordinates and position are known and perpendicular to the hole-making direction of the end actuator of the automatic drilling and riveting mac...
Embodiment 3
[0035] This device is used for robot hole making positioning and normal direction measurement, and is characterized in that: the structure of the reflector driving mechanism (3) is: the reflector (2) is connected to a fixed fixture with a synchronous trigger module, and the synchronous trigger module includes limit position switch sensor and limit switch sensor driving circuit; the mirror drive mechanism (3) is connected with the embedded system to control the state change of the driven mirror (2); during hole positioning and normal measurement, the mirror ( 2) After receiving the driving trigger signal, it will extend from -90° to -45°; when the end effector (4) performs hole making, the mirror (2) will shrink from -45° to -90°.
PUM
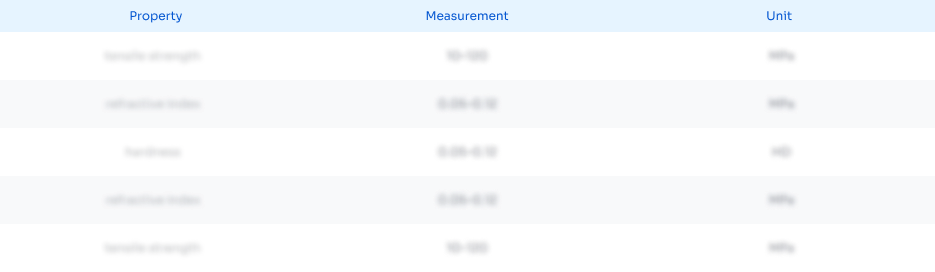
Abstract
Description
Claims
Application Information

- R&D Engineer
- R&D Manager
- IP Professional
- Industry Leading Data Capabilities
- Powerful AI technology
- Patent DNA Extraction
Browse by: Latest US Patents, China's latest patents, Technical Efficacy Thesaurus, Application Domain, Technology Topic, Popular Technical Reports.
© 2024 PatSnap. All rights reserved.Legal|Privacy policy|Modern Slavery Act Transparency Statement|Sitemap|About US| Contact US: help@patsnap.com