Method for preparing cable insulating layer and extruder
A technology of cable insulation and extruder, which is applied in the direction of organic insulators, plastic/resin/wax insulators, etc., which can solve the problem of warehouse management time, management pressure and cost increase, black sheath material performance cannot be guaranteed, black sheath material Problems such as production quality problems, to achieve the effect of reducing production energy consumption and storage management costs, saving production time, and avoiding cleaning
- Summary
- Abstract
- Description
- Claims
- Application Information
AI Technical Summary
Problems solved by technology
Method used
Image
Examples
Embodiment 1
[0038] This example provides a method for preparing the cable insulation layer. Add the natural color cable insulation material and color masterbatch to the extruder respectively. 180°C, 160~180°C, 165~180°C, extruded to prepare cable insulation layer. Among them, the mass ratio of natural color cable insulation material to color masterbatch is 100:1.
[0039] The raw material formula of the cable insulating material of preparing the natural color in the present embodiment comprises:
[0040]
[0041] The method for preparing the cable insulation layer also includes the step of preparing the cable insulation material of the above natural color: PVC resin, dioctyl phthalate, epoxy soybean oil, chlorinated paraffin 52#, dioctyl terephthalate, kaolin , light calcium carbonate, stabilizer 1984, ethylene bis stearic acid amide, barium stearate, and stearic acid are added to the mixer and mixed, and discharged from the mixer at 110 ° C ~ 115 ° C, and then at 116 Plasticizing an...
Embodiment 2
[0055] This example provides a method for preparing the cable insulation layer. Add the natural color cable insulation material and color masterbatch to the extruder respectively. 180°C, 160~180°C, 165~180°C, extruded to prepare cable insulation layer. Among them, the mass ratio of natural color cable insulation material to color masterbatch is 150:1.
[0056] The raw material formula for preparing the natural color cable insulation material includes:
[0057]
[0058] The method for preparing the cable insulation layer also includes the step of preparing the cable insulation material of the above natural color: PVC resin, dioctyl phthalate, epoxy soybean oil, chlorinated paraffin 52#, dioctyl terephthalate, kaolin , light calcium carbonate, stabilizer 1984, ethylene bis stearic acid amide, barium stearate, and stearic acid are added to the mixer and mixed, and discharged from the mixer at 110 ° C ~ 115 ° C, and then at 116 Plasticizing and granulating in a twin-screw mac...
Embodiment 3
[0062] This example provides a method for preparing the cable insulation layer. Add the natural color cable insulation material and color masterbatch to the extruder respectively. 180°C, 160~180°C, 165~180°C, extruded to prepare cable insulation layer. Among them, the mass ratio of natural color cable insulation material to color masterbatch is 50:1.
[0063] The raw material formula for preparing the natural color cable insulation material includes:
[0064]
[0065] The method for preparing the cable insulation layer also includes the step of preparing the cable insulation material of the above natural color: PVC resin, dioctyl phthalate, epoxy soybean oil, chlorinated paraffin 52#, dioctyl terephthalate, kaolin , light calcium carbonate, stabilizer 1984, ethylene bis stearic acid amide, barium stearate, and stearic acid are added to the mixer and mixed, and discharged from the mixer at 110 ° C ~ 115 ° C, and then at 116 Plasticizing and granulating in a twin-screw mach...
PUM
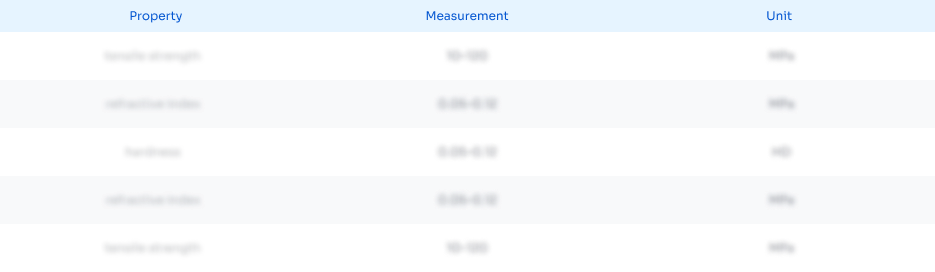
Abstract
Description
Claims
Application Information

- R&D
- Intellectual Property
- Life Sciences
- Materials
- Tech Scout
- Unparalleled Data Quality
- Higher Quality Content
- 60% Fewer Hallucinations
Browse by: Latest US Patents, China's latest patents, Technical Efficacy Thesaurus, Application Domain, Technology Topic, Popular Technical Reports.
© 2025 PatSnap. All rights reserved.Legal|Privacy policy|Modern Slavery Act Transparency Statement|Sitemap|About US| Contact US: help@patsnap.com