Grinding and polishing robot clamp system capable of being switched between 0-degree working state and 90-degree working state and using method thereof
A technology for robot fixtures and switching work, which is applied in the direction of grinding workpiece supports, etc., to achieve the effects of flexible and intelligent movement, shortening the process flow, and reducing the equipment footprint
- Summary
- Abstract
- Description
- Claims
- Application Information
AI Technical Summary
Problems solved by technology
Method used
Image
Examples
Embodiment Construction
[0034] like Figures 1 to 9 As shown, a grinding and polishing robot fixture system with two switching working states of 0 degrees and 90 degrees according to the present invention includes a fixture head assembly 1 and a tightening drive that is tightly connected with the fixture head to drive the fixture head assembly to work. Assembly 2. Rotary drive assembly 3 for driving and controlling the overall switching of the tensioning drive assembly and the fixture head assembly in two working states of 0° and 90°, and a positioning drive for restricting the overall positioning of the tensioning drive assembly and the clamp head assembly Component 4.
[0035] like figure 1 , 3 As shown, the clamp head assembly 1 includes a clamp head sleeve 11, a push rod body 12 installed in the clamp head sleeve, a push steel ball 13 and a spring chuck 14; the tightening drive assembly 2 includes There is a tensioning cylinder 21 and a tensioning connection seat 22, wherein: one end of the te...
PUM
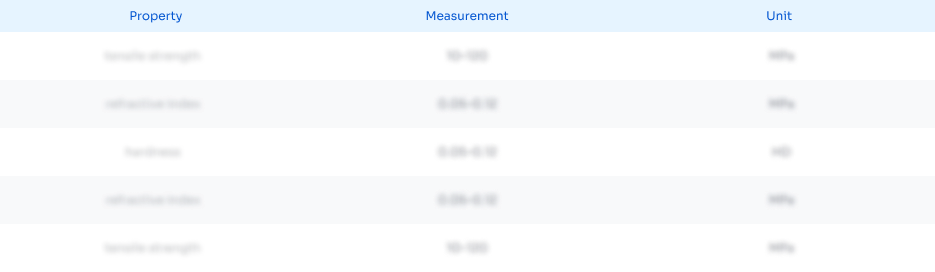
Abstract
Description
Claims
Application Information

- R&D
- Intellectual Property
- Life Sciences
- Materials
- Tech Scout
- Unparalleled Data Quality
- Higher Quality Content
- 60% Fewer Hallucinations
Browse by: Latest US Patents, China's latest patents, Technical Efficacy Thesaurus, Application Domain, Technology Topic, Popular Technical Reports.
© 2025 PatSnap. All rights reserved.Legal|Privacy policy|Modern Slavery Act Transparency Statement|Sitemap|About US| Contact US: help@patsnap.com