A Real-time Compensation Method for Comprehensive Error of CNC Machine Tool
A real-time compensation and comprehensive error technology, applied in the field of machine tool error compensation, can solve problems such as difficulty in obtaining perfect thermal error information, high machine tool processing time, high cost, and expensive error compensation, so as to save labor and machine tool downtime, modeling Convenient and economical, good model fitting performance
- Summary
- Abstract
- Description
- Claims
- Application Information
AI Technical Summary
Problems solved by technology
Method used
Image
Examples
Embodiment 1
[0061] Such as Figure 1-7 As shown, a real-time compensation method for comprehensive errors of CNC machine tools includes the following steps:
[0062] S1. Measure the displacement error of each axis of the machine tool to be compensated according to the selected geometric error identification method, and then identify the various geometric errors of the translation axis of the machine tool;
[0063] S2. Establishing a guide rail thermal error model of the machine tool to be compensated;
[0064] S3. Establishing a Z-direction offset error model of the worktable of the machine tool to be compensated;
[0065] S4. Collect the temperature data at the key points of the heat source of the machine tool, and determine the position information of the processed parts on the workbench;
[0066] S5. Bring the collected temperature at the key points of the machine tool into the thermal error model of the machine tool guide rail to obtain the real-time geometric error of the machine t...
PUM
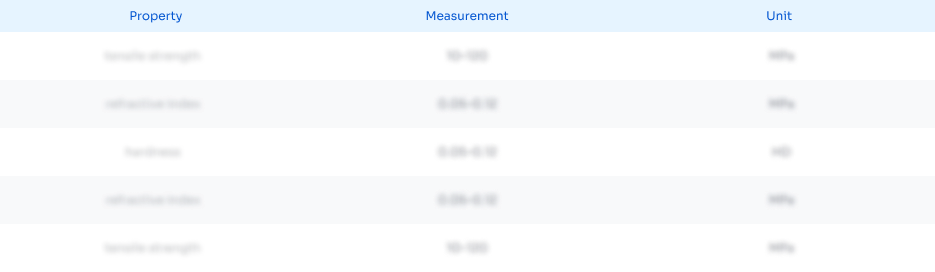
Abstract
Description
Claims
Application Information

- R&D
- Intellectual Property
- Life Sciences
- Materials
- Tech Scout
- Unparalleled Data Quality
- Higher Quality Content
- 60% Fewer Hallucinations
Browse by: Latest US Patents, China's latest patents, Technical Efficacy Thesaurus, Application Domain, Technology Topic, Popular Technical Reports.
© 2025 PatSnap. All rights reserved.Legal|Privacy policy|Modern Slavery Act Transparency Statement|Sitemap|About US| Contact US: help@patsnap.com