A production method for controlling warped skin defects at the edge of ultra-low carbon steel
A production method and technology of ultra-low carbon steel, which is applied in the field of steel rolling, can solve problems such as warped skin defects at the edge of slabs, prevent warped skin defects, reduce edge temperature drop, and avoid low edge temperature Effect
- Summary
- Abstract
- Description
- Claims
- Application Information
AI Technical Summary
Problems solved by technology
Method used
Image
Examples
Embodiment 1
[0077] The ultra-low carbon steel grade is SDC03, with a specification of 4.5*1328mm.
[0078] Table 1. Steel composition list
[0079]
[0080] production method:
[0081] The heating time in the furnace is 192min, the tapping temperature is 1102°C, the water pressure of the descaling operation after exiting the heating furnace is 20.2Mpa, the descaling rate is 1.4m / s, the width adjustment of the sizing machine is 36mm, and the rough rolling is rolled in 8 passes No descaling was performed in the last two passes, the exit temperature of rough rolling was 848°C, and the entrance temperature of finish rolling was 843°C. Put the heat preservation cover between the rough rolling and the finishing rolling, turn off the cooling water of the work rolls and the descaling between the racks, and put in the rolling lubrication and anti-stripping water of F1-F4, and the warping defect at the edge of the strip is obviously improved.
Embodiment 2
[0083] Involving steel type SDC03, specification 5.0*1406mm
[0084] Table 2. Steel composition table
[0085]
[0086] Control Method:
[0087] The heating time in the furnace is 187min, the tapping temperature is 1097°C, the descaling pressure after exiting the heating furnace is 20.3Mpa, the descaling rate is 1.33m / s, the width adjustment of the sizing machine is 48mm, rough rolling and co-rolling are 8 passes, and the last 2 There is no descaling in the pass, the exit temperature of rough rolling is 857°C, and the entry temperature of finish rolling is 850°C. The insulation cover is put in between the rough rolling and the finishing rolling, the cooling water of the work rolls and the descaling between the racks are closed, and the rolling lubrication and anti-stripping water of F1-F4 are put in. The warped skin defect at the edge of the strip is obviously improved.
[0088] One or more technical solutions provided in the embodiments of this application have at least...
PUM
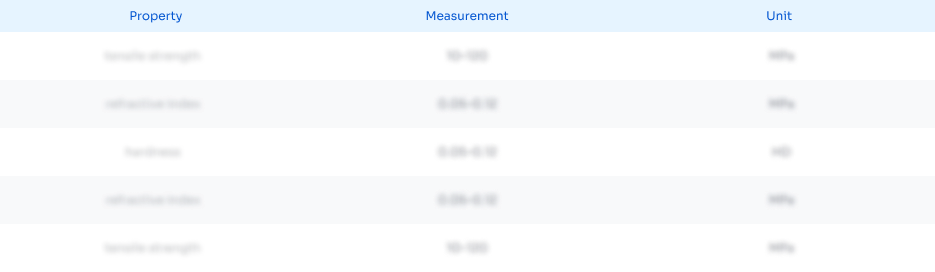
Abstract
Description
Claims
Application Information

- R&D
- Intellectual Property
- Life Sciences
- Materials
- Tech Scout
- Unparalleled Data Quality
- Higher Quality Content
- 60% Fewer Hallucinations
Browse by: Latest US Patents, China's latest patents, Technical Efficacy Thesaurus, Application Domain, Technology Topic, Popular Technical Reports.
© 2025 PatSnap. All rights reserved.Legal|Privacy policy|Modern Slavery Act Transparency Statement|Sitemap|About US| Contact US: help@patsnap.com