Riveting die used for ball head rivet and sheet metal part
A technology for sheet metal parts and sheet metal parts, which is applied in the field of riveting molds, can solve the problems that the ejection force and torsion force cannot meet the requirements of customers, the product quality cannot be guaranteed, and the product stability is poor. The effect of easy access
- Summary
- Abstract
- Description
- Claims
- Application Information
AI Technical Summary
Problems solved by technology
Method used
Image
Examples
Embodiment 1
[0022] A riveting die for ball rivets and sheet metal parts, the structure of which is as follows figure 1 As shown, it includes an upper mold 1 and a lower mold 2. The lower surface of the upper mold 1 is provided with a riveting punch 12 for pressing the ball rivet 3 and the sheet metal to realize riveting, and the upper surface of the lower mold 2 is processed with a clamping arrangement. The clamping block assembly of the ball rivet 3 and the sheet metal part, the clamping block assembly includes a static clamping block 21 and a movable clamping block 22 that are butted and matched with each other to form a riveting cavity that matches the ball rivet 3 and the sheet metal part, and the lower die 2 is provided with There is a guide hole along the horizontal direction, and a push rod 23 moving along it is installed in the guide hole. One end of the push rod 23 extends out of the lower die 2, and the other end is connected to the movable clamp block 22, and drives the movable ...
Embodiment 2
[0025] On the basis of embodiment 1, this embodiment is further set to:
[0026] A baffle 25 is connected to the end of the push rod 23 , and a return spring 24 is also provided between the baffle 25 and the lower die 2 .
Embodiment 3
[0028] On the basis of embodiment 2, this embodiment is further set to:
[0029] The side of lower die 2 is also fixedly provided with a positioning seat, and a clamping cam 26 is rotated on the positioning seat. The cam surface of this clamping cam 26 is against the baffle plate 25, and the clamping cam 26 is also equipped with a handle 27 outwards.
PUM
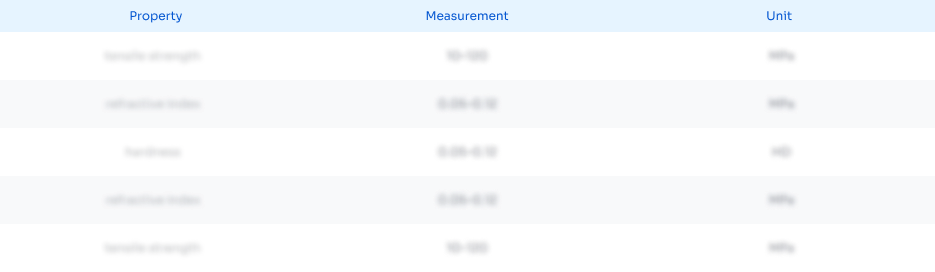
Abstract
Description
Claims
Application Information

- R&D
- Intellectual Property
- Life Sciences
- Materials
- Tech Scout
- Unparalleled Data Quality
- Higher Quality Content
- 60% Fewer Hallucinations
Browse by: Latest US Patents, China's latest patents, Technical Efficacy Thesaurus, Application Domain, Technology Topic, Popular Technical Reports.
© 2025 PatSnap. All rights reserved.Legal|Privacy policy|Modern Slavery Act Transparency Statement|Sitemap|About US| Contact US: help@patsnap.com