Method for preparing high-quality superfine and light calcium carbonate by taking gypsum as raw material
A technology of light calcium carbonate and calcium carbonate, applied in the direction of calcium carbonate/strontium/barium, chemical instruments and methods, sustainable manufacturing/processing, etc., can solve the problems of large energy consumption and energy consumption, and achieve energy saving and high performance High, the effect of improving processability and mechanical properties
- Summary
- Abstract
- Description
- Claims
- Application Information
AI Technical Summary
Problems solved by technology
Method used
Examples
Embodiment 1
[0026] A method for preparing high-quality ultra-fine light calcium carbonate using gypsum as a raw material includes the following steps:
[0027] (1) Using gypsum as raw material, add appropriate amount of water to make a slurry with a calcium sulfate solid content of 40%;
[0028] (2) Add the calcium sulfate slurry of step (1) to 0.8 times the mass of calcium sulfate sodium carbonate, add 1% of the mass of calcium sulfate surfactant, stir at room temperature for 2 hours, and react to obtain a mixed slurry of sodium sulfate and calcium carbonate;
[0029] (3) Filter the slurry of step (2), and store the filtrate and the precipitate separately;
[0030] (4) Pass the filtrate of step (3) into carbon dioxide at room temperature for 30 minutes, filter again, put the filtrate into a storage tank for storage, and combine the obtained precipitate with the precipitate of step (3) and put it in a centrifuge for dehydration;
[0031] (5) Put the dehydrated precipitate in step (4) into a drying ...
Embodiment 2
[0041] A method for preparing high-quality ultra-fine light calcium carbonate using gypsum as a raw material includes the following steps:
[0042] (1) Using gypsum as raw material, add appropriate amount of water to make a slurry with a calcium sulfate solid content of 50%;
[0043] (2) Add the calcium sulfate slurry of step (1) to the amount of calcium sulfate substance 1 time sodium carbonate, add 2% calcium sulfate surface active agent, stir at room temperature for 3 hours, and react to obtain a sodium sulfate and calcium carbonate mixed slurry ;
[0044] (3) Filter the slurry of step (2), and store the filtrate and the precipitate separately;
[0045] (4) Pass the filtrate of step (3) into carbon dioxide at room temperature for 35 minutes, filter again, put the filtrate into a storage tank for storage, and combine the obtained precipitate with the precipitate of step (3) and put it in a centrifuge for dehydration;
[0046] (5) Put the dehydrated precipitate in step (4) into a dryi...
Embodiment 3
[0056] A method for preparing high-quality ultra-fine light calcium carbonate using gypsum as a raw material includes the following steps:
[0057] (1) Using gypsum as raw material, add appropriate amount of water to make a slurry with a calcium sulfate solid content of 60%;
[0058] (2) Add the calcium sulfate slurry of step (1) to 1.2 times the mass of calcium sulfate sodium carbonate, add 3% of the calcium sulfate mass surfactant, and stir at room temperature for 4 hours to react to obtain a mixed slurry of sodium sulfate and calcium carbonate;
[0059] (3) Filter the slurry of step (2), and store the filtrate and the precipitate separately;
[0060] (4) Pass the filtrate of step (3) into carbon dioxide at room temperature for 40 minutes, filter again, put the filtrate into a storage tank, and combine the obtained precipitate with the precipitate of step (3) and put it in a centrifuge for dehydration;
[0061] (5) Put the dehydrated precipitate in step (4) into a drying furnace, and ...
PUM
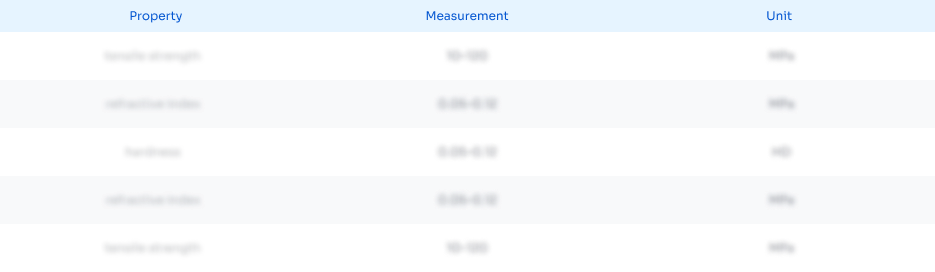
Abstract
Description
Claims
Application Information

- R&D
- Intellectual Property
- Life Sciences
- Materials
- Tech Scout
- Unparalleled Data Quality
- Higher Quality Content
- 60% Fewer Hallucinations
Browse by: Latest US Patents, China's latest patents, Technical Efficacy Thesaurus, Application Domain, Technology Topic, Popular Technical Reports.
© 2025 PatSnap. All rights reserved.Legal|Privacy policy|Modern Slavery Act Transparency Statement|Sitemap|About US| Contact US: help@patsnap.com