Film synchronous embossing device
A technology of embossing and thin film, which is applied in the field of synchronous embossing device for thin film, which can solve the problems of long materials, waste, and the need for multiple tests to meet the requirements, etc.
- Summary
- Abstract
- Description
- Claims
- Application Information
AI Technical Summary
Problems solved by technology
Method used
Image
Examples
Embodiment 1
[0021] like Figure 1-5 As shown, a synchronous embossing device for a film in this embodiment includes a first support 10, a rubber roller 11 arranged on the first support 10, a second support 20, and an embossing roller arranged on the second support 20 21. The surface of the embossing roller 21 is provided with the same uneven texture as the film pattern, the rubber roller 11 and the embossing roller 21 are respectively connected to the first motor 40 and the second motor 41, the first motor 40 and the The second motor 41 independently controls the rotation direction and speed of the rubber roller 11 and the embossing roller 21 respectively, and the embossing roller 21 can move relative to the rubber roller 11 in four directions, front, rear, left, and right on the horizontal plane. In the traditional embossing device, the embossing roller adopts the active transmission method, while the rubber roller adopts the passive transmission method. It is necessary to adjust the cor...
Embodiment 2
[0023] like Figure 1-5 As shown, the rubber roller 11 is connected to the first motor 40 through the first universal coupling 42 , and the embossing roller 21 is connected to the second motor 41 through the second universal coupling 43 . The distance between the embossing roller 21 and the rubber roller 11 needs to be adjusted back and forth, and the position of the second motor 41 is fixed, so the distance between the second motor 41 and the embossing roller 21 will have a certain change. The universal coupling 43 is scalable, so that the second motor 41 can control the rotation direction and rotation speed of the embossing roller 21 without changing the position of the second motor 41 . In order to meet wider requirements for the synchronous embossing device of this embodiment, the first telescopic rod 42 is also set in this way.
Embodiment 3
[0025] like Figure 1-5 As shown, in this embodiment, the structural device for the embossing roller 21 to move left and right relative to the rubber roller 11 is perfected. The rubber roller 11 is fixed on the first bracket 10 through the fixing seat 50, the embossing roller 21 is arranged on the second bracket 20, and the first bracket 10 is provided with a left and right moving slide rail 13, so The second support 20 described above is connected to the first support 10 through the left and right moving slide rails 13, and the first support 10 can slide on the left and right moving slide rails 13 to adjust the left and right relative positions of the embossing roller 21 and the rubber roller 11. Since the embossing roller 21 is arranged on the second support 20, and the rubber roller 11 is fixed on the first support 10, it is only necessary to adjust the left and right positions between the first support 10 and the second space 20, and the The purpose of adjusting the left ...
PUM
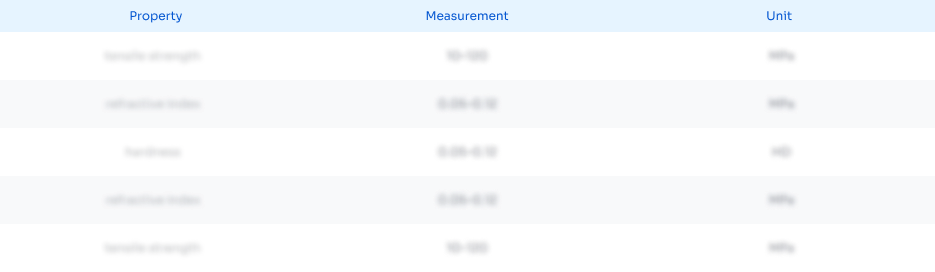
Abstract
Description
Claims
Application Information

- Generate Ideas
- Intellectual Property
- Life Sciences
- Materials
- Tech Scout
- Unparalleled Data Quality
- Higher Quality Content
- 60% Fewer Hallucinations
Browse by: Latest US Patents, China's latest patents, Technical Efficacy Thesaurus, Application Domain, Technology Topic, Popular Technical Reports.
© 2025 PatSnap. All rights reserved.Legal|Privacy policy|Modern Slavery Act Transparency Statement|Sitemap|About US| Contact US: help@patsnap.com