Electric servo system stiffness modeling method
A system stiffness and modeling method technology, applied in the field of electric servo system, can solve the problems of low servo stiffness, affecting system positioning accuracy, large loss of motion, etc., and achieve the effect of improving servo stiffness, reasonable mass distribution, and improving robustness
- Summary
- Abstract
- Description
- Claims
- Application Information
AI Technical Summary
Problems solved by technology
Method used
Image
Examples
Embodiment Construction
[0022] as attached figure 1 As shown, an electric servo system stiffness modeling method includes the following steps:
[0023] Step 1: Setting up the modeling foundation
[0024] Matlab / Simulink establishes the control system of the electric rudder system;
[0025] Step 2: Establish model connection relationship
[0026] According to the situation of the object to be modeled, the model connection relationship is established, and the model prototype is implemented by calling the modules in Matlab / Simulink, especially Simscape;
[0027] When building a gear model, in addition to the conventional circuit, the upper and lower clearances, contact stiffness, contact damping, and initial angular position of the two rotating parts are also added. The upper and lower gaps, contact stiffness, contact damping, and initial angle position information of the above two rotating parts are set to initial values as required.
[0028] When building the model of the ball screw pair, in add...
PUM
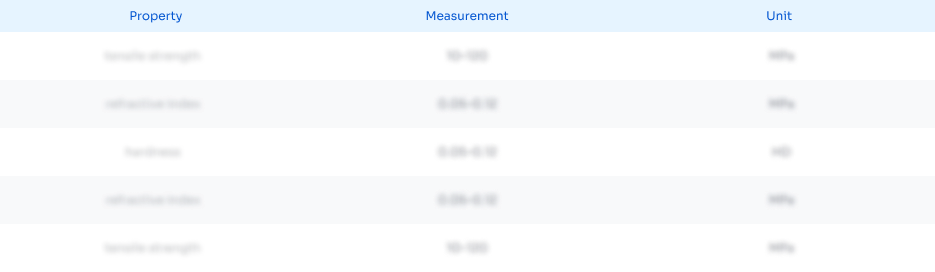
Abstract
Description
Claims
Application Information

- Generate Ideas
- Intellectual Property
- Life Sciences
- Materials
- Tech Scout
- Unparalleled Data Quality
- Higher Quality Content
- 60% Fewer Hallucinations
Browse by: Latest US Patents, China's latest patents, Technical Efficacy Thesaurus, Application Domain, Technology Topic, Popular Technical Reports.
© 2025 PatSnap. All rights reserved.Legal|Privacy policy|Modern Slavery Act Transparency Statement|Sitemap|About US| Contact US: help@patsnap.com