High-precision guide rail straightness calibration structure and method
A straightness and high-precision technology, used in linear motion bearings, angle/taper measurement, bearings, etc., to solve the problems of complex equipment structure, adjustable position, few directions to meet work requirements, and single adjustment and control means.
- Summary
- Abstract
- Description
- Claims
- Application Information
AI Technical Summary
Problems solved by technology
Method used
Image
Examples
Embodiment 1
[0025] Example 1, such as Figure 1~4 As shown, a calibration structure for the straightness of a high-precision guide rail includes a base 1, a marble parallel ruler 2, a guide rail 3, a slider 4, a wedge 5, a top tightening block 6, an adjusting screw 7 and a fixing screw 8, and the marble parallel ruler 2 Installed on one side of the base 1, the base 1 is provided with an installation groove 11 and an adjustment groove 12 connected with the installation groove 11, the guide rail 3 is locked in the installation groove 11 by the fixing screw 8, and the guide rail 3 is closely attached to the installation groove 11 On the side wall, the slider 4 is slidably arranged on the guide rail 3, and a dial indicator 9 for calibrating the straightness of the guide rail 3 is placed on the top of the slider 4. The wedge 5 and the top tightening block 6 are all installed in the adjustment groove 12, and the top tightening block One end surface of 6 abuts against the guide rail 3 , the othe...
Embodiment 2
[0029] Embodiment 2, realize the calibration method to guide rail straightness by the structure of embodiment 1, comprise the following steps:
[0030] 1) Install the marble parallel ruler 2 on the side of the base 1, make the marble parallel ruler 2 and the guide rail 3 in a parallel state as much as possible, and place the dial gauge 9 on the slider 4 slidingly connected with the guide rail 3, so that the dial gauge 9 The measuring head is in contact with the side wall of the marble parallel ruler 2. At this time, measure the reading at point A of one end of the marble parallel ruler 2, then move the slider 4 to the other end, and measure the marble parallel ruler 2 without moving at the position of the dial indicator 9. The value of point B at one end, if the readings of points A and B are consistent, it means that the straightness of the marble has been calibrated, if the readings of points A and B are inconsistent, it means that the straightness of the marble is not calibr...
PUM
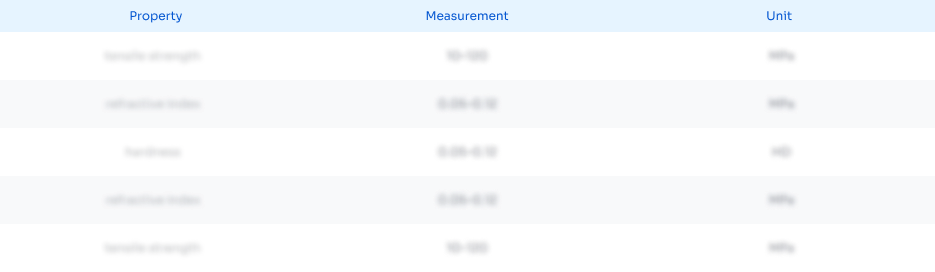
Abstract
Description
Claims
Application Information

- Generate Ideas
- Intellectual Property
- Life Sciences
- Materials
- Tech Scout
- Unparalleled Data Quality
- Higher Quality Content
- 60% Fewer Hallucinations
Browse by: Latest US Patents, China's latest patents, Technical Efficacy Thesaurus, Application Domain, Technology Topic, Popular Technical Reports.
© 2025 PatSnap. All rights reserved.Legal|Privacy policy|Modern Slavery Act Transparency Statement|Sitemap|About US| Contact US: help@patsnap.com