Ship propeller excitation force friction reduction device
A propeller and excitation force technology, applied in the direction of rotating propellers, rotary propellers, etc., can solve the problems of difficulty in designing energy-consuming blade vibration and transmission devices, easily affecting the hydrodynamic performance of the propeller, and amplifying the propeller excitation force. , to achieve the effect of small additional mass, simple design and vibration attenuation
- Summary
- Abstract
- Description
- Claims
- Application Information
AI Technical Summary
Problems solved by technology
Method used
Image
Examples
Embodiment Construction
[0026] In order to have a clearer understanding of the technical features, purposes and effects of the present invention, the specific implementation manners of the present invention will now be described in detail with reference to the accompanying drawings.
[0027] Such as Figure 1-6 Shown is a ship propeller excitation force friction reduction device according to a preferred embodiment of the present invention, including a propeller and a damping treatment device 30 installed at the end of the propeller hub 20, and the propeller blade 10 and the propeller hub 20 are integrally formed. The damping treatment device 30 includes a frictional damping ring 31 , a pressing plate 32 and a fastener 33 , the frictional damping ring 31 is an annular circular truncated structure, and the pressing plate 32 is an annular cylindrical structure. The end of the propeller hub 20 is axially provided with a conical groove 21 that matches the shape of the friction damping ring 31 . The conica...
PUM
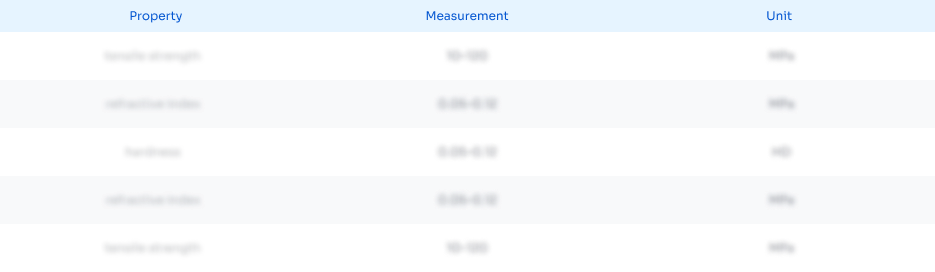
Abstract
Description
Claims
Application Information

- R&D Engineer
- R&D Manager
- IP Professional
- Industry Leading Data Capabilities
- Powerful AI technology
- Patent DNA Extraction
Browse by: Latest US Patents, China's latest patents, Technical Efficacy Thesaurus, Application Domain, Technology Topic, Popular Technical Reports.
© 2024 PatSnap. All rights reserved.Legal|Privacy policy|Modern Slavery Act Transparency Statement|Sitemap|About US| Contact US: help@patsnap.com