Production method of particleboard
A production method and particle board technology, which are applied in the field of wood processing, can solve the problems of high production cost, high energy consumption, low efficiency, etc., and achieve the effects of reducing hot pressing time, improving hot pressing forming rate and reducing production cost.
- Summary
- Abstract
- Description
- Claims
- Application Information
AI Technical Summary
Problems solved by technology
Method used
Image
Examples
Embodiment 1
[0032] A kind of production method of chipboard, is made up of following steps:
[0033] (1) Preparation of shavings: select the raw twig wood, cut it with a chipper, and then screen it with a screening machine to remove unqualified wood chips, bark, sand and metal debris to obtain twig wood slices; select broken veneer , after crushing with a hammer planer, then screen with a screening machine to obtain broken veneer wood chips; the branch wood slices and broken veneer wood chips are sent to a planer for planing to obtain flake shavings;
[0034] (2) Drying and screening: the flaky shavings are sent into a single-channel flue gas dryer for drying, the drying temperature is 130°C, and the moisture content of the dried flaky shavings is 1.5%; the dried flaky shavings are screened into The surface layer of fine shavings and the core layer of coarse shavings, and the surface layer of fine shavings and the core layer of coarse shavings are insulated at a temperature of 45°C; the s...
Embodiment 2
[0046] The preparation method of the urea-formaldehyde resin glue of present embodiment and embodiment 1 is identical, and difference is:
[0047] A kind of production method of chipboard, is made up of following steps:
[0048] (1) Preparation of shavings: select the raw twig wood, cut it with a chipper, and then screen it with a screening machine to remove unqualified wood chips, bark, sand and metal debris to obtain twig wood slices; select broken veneer , after crushing with a hammer planer, then screen with a screening machine to obtain broken veneer wood chips; the branch wood slices and broken veneer wood chips are sent to a planer for planing to obtain flake shavings;
[0049] (2) Drying and screening: the flaky shavings are sent into a single-channel flue gas dryer for drying, the drying temperature is 160° C., and the moisture content of the dried flaky shavings is 2.5%; the dried flaky shavings are screened into The surface layer of fine shavings and the core layer...
Embodiment 3
[0055] The preparation method of present embodiment and embodiment 1 and other processing parameters are identical, and difference is:
[0056] Step (5) hot pressing forming: hot pressing the pre-pressed slab with a continuous flat pressing hot press to obtain a raw board; the hot pressing forming stage consists of a high pressure hot pressing zone, a low pressure hot pressing zone and a secondary pressurization The composition of the hot-press zone, the pressure of the high-pressure hot-press zone is 3N / mm 2 , the temperature is 230°C; the low-pressure hot-press zone consists of a front section and a back section, and the pressure of the front section is 2.2N / mm 2 , the temperature is 230°C; the pressure in the latter section is 1.5N / mm 2 , the temperature is 210°C; the pressure in the secondary pressurized hot pressing zone is 1.0N / mm 2 , the temperature is 190° C.; the thermal compression factor is 5.5 s / mm.
PUM
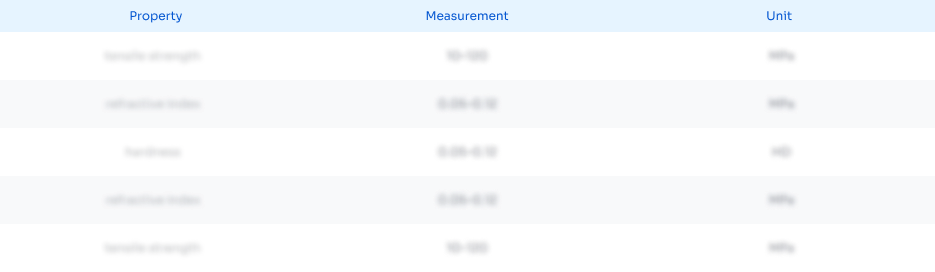
Abstract
Description
Claims
Application Information

- R&D
- Intellectual Property
- Life Sciences
- Materials
- Tech Scout
- Unparalleled Data Quality
- Higher Quality Content
- 60% Fewer Hallucinations
Browse by: Latest US Patents, China's latest patents, Technical Efficacy Thesaurus, Application Domain, Technology Topic, Popular Technical Reports.
© 2025 PatSnap. All rights reserved.Legal|Privacy policy|Modern Slavery Act Transparency Statement|Sitemap|About US| Contact US: help@patsnap.com