Inductive sensor calibration method and device for capacitive sensor displacement compensation
A technology of capacitive sensor and inductive sensor, applied in the field of precision measurement, can solve the problems of low accuracy, small calibration stroke, small calibration stroke, etc., to ensure the calibration accuracy, improve the calibration stroke, and eliminate errors.
- Summary
- Abstract
- Description
- Claims
- Application Information
AI Technical Summary
Problems solved by technology
Method used
Image
Examples
Embodiment Construction
[0021] The present invention will be described in further detail below in conjunction with the accompanying drawings:
[0022] A method and device for calibrating an inductive sensor for displacement compensation of a capacitance sensor. The method and device are as follows: the whole device is mainly divided into a displacement reference instrument, a displacement transmission mechanism and a calibrated displacement sensor. The entire device is placed on a vibration isolation platform and placed in a constant temperature environment. The calibrated displacement sensor adopts the inductive displacement sensor 3, and the inductive displacement sensor 3 is clamped and fixed by the sensor clamping arm 2. The position of the inductive displacement sensor 3 is adjusted to ensure the movement axis of the stylus 3a of the inductive displacement sensor 3 and the dual-frequency laser The optical axis of the measuring beam 10a of the interferometer 10 is collinear, the sensor support 1 is ...
PUM
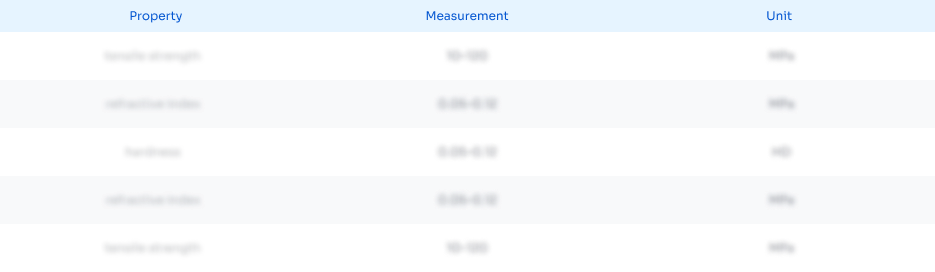
Abstract
Description
Claims
Application Information

- R&D Engineer
- R&D Manager
- IP Professional
- Industry Leading Data Capabilities
- Powerful AI technology
- Patent DNA Extraction
Browse by: Latest US Patents, China's latest patents, Technical Efficacy Thesaurus, Application Domain, Technology Topic, Popular Technical Reports.
© 2024 PatSnap. All rights reserved.Legal|Privacy policy|Modern Slavery Act Transparency Statement|Sitemap|About US| Contact US: help@patsnap.com