Method for manufacturing flanges of wind turbine blade girder mould and wind turbine blade girder mould
A technology for wind power blades and a manufacturing method, which can be applied to household appliances, other household appliances, household components, etc., can solve problems such as lack of double baffles
- Summary
- Abstract
- Description
- Claims
- Application Information
AI Technical Summary
Problems solved by technology
Method used
Image
Examples
Embodiment Construction
[0045] The present invention is further illustrated below by means of examples, but the present invention is not limited to the scope of the examples.
[0046] Such as Figure 1 to Figure 2 As shown, a method for manufacturing a rib of a wind power blade main girder mold includes the following steps:
[0047] S1. According to the rib position of the main beam, mark the positioning plate installation area 11 and the rib installation area 12 on the mold body 1;
[0048] S2, place the positioning plate 2 in the positioning plate installation area 11, and the surface of the positioning plate 2 and the rib installation area 12 forms an included angle area 3;
[0049] S3. Cover the surface of the angled area 3 with a layer of sizing cloth, paste a layer of liquid sizing agent on the sizing cloth, and form a solidified layer 4 with the sizing cloth after the liquid sizing agent solidifies;
[0050] S4, cutting the cured layer 4 according to the set shape;
[0051] S5, set baffles ...
PUM
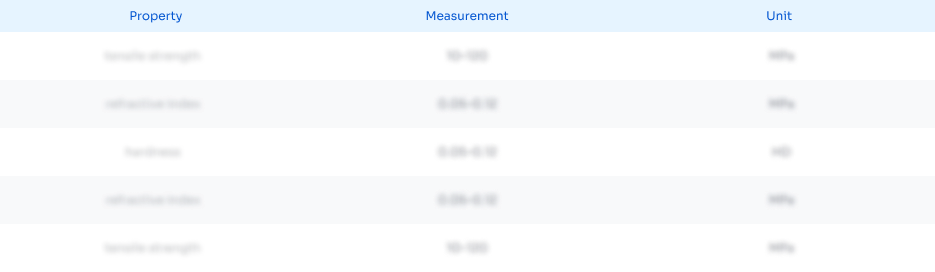
Abstract
Description
Claims
Application Information

- R&D
- Intellectual Property
- Life Sciences
- Materials
- Tech Scout
- Unparalleled Data Quality
- Higher Quality Content
- 60% Fewer Hallucinations
Browse by: Latest US Patents, China's latest patents, Technical Efficacy Thesaurus, Application Domain, Technology Topic, Popular Technical Reports.
© 2025 PatSnap. All rights reserved.Legal|Privacy policy|Modern Slavery Act Transparency Statement|Sitemap|About US| Contact US: help@patsnap.com