Workpiece residual stress detection method based on ultrasonic driven boring
A residual stress and detection method technology, applied in the direction of force/torque/work measuring instruments, measuring devices, instruments, etc., can solve the problems of additional cutting stress, large cutting force, uncontrollable applied force, etc., to reduce additional stress and Effects of microplastic deformation, reduced contact time, and reduced error value
- Summary
- Abstract
- Description
- Claims
- Application Information
AI Technical Summary
Problems solved by technology
Method used
Image
Examples
Embodiment Construction
[0031] Embodiments of the present invention will be described in further detail below in conjunction with the accompanying drawings.
[0032] Figure 1 to Figure 3 Shown is the structural representation of the present invention.
[0033] The reference signs therein are: flat drill floor 1, installation base 11, positioning boss 11a, adjusting support foot 12, ultrasonic electric spindle 2, ultrasonic electric spindle drive module 21, ultrasonic drive drill bit 22, fixed ferrule 3, lifting Guide part 3 a , positioning rack 31 , positioning drive motor 32 , and positioning knob 33 .
[0034] A drilling device for detecting residual stress by the blind hole method of the present invention comprises a flat drill floor 1, the flat drill floor 1 is fixed with an installation base 11, and the installation base 11 is detachably installed with an ultrasonic electric spindle 2 and an ultrasonic The electric spindle drive module 21, the ultrasonic electric spindle 2 is connected with a...
PUM
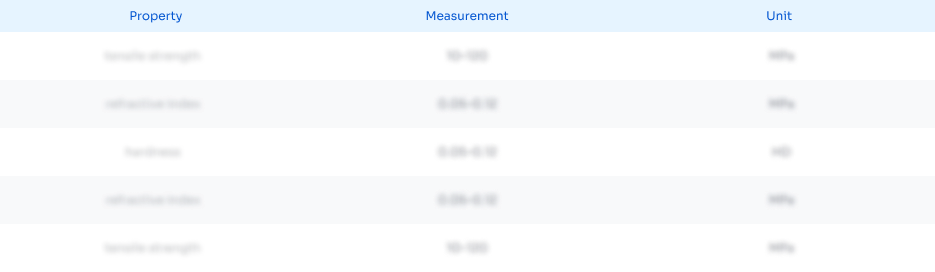
Abstract
Description
Claims
Application Information

- R&D
- Intellectual Property
- Life Sciences
- Materials
- Tech Scout
- Unparalleled Data Quality
- Higher Quality Content
- 60% Fewer Hallucinations
Browse by: Latest US Patents, China's latest patents, Technical Efficacy Thesaurus, Application Domain, Technology Topic, Popular Technical Reports.
© 2025 PatSnap. All rights reserved.Legal|Privacy policy|Modern Slavery Act Transparency Statement|Sitemap|About US| Contact US: help@patsnap.com