Casting film cutting edge material smashing device
A processing device and casting film technology, which is applied in metal processing and other directions, can solve the problems of unrealistic chip processing methods, and achieve the effects of efficient and fast processing, neat cutting, and reasonable structure.
- Summary
- Abstract
- Description
- Claims
- Application Information
AI Technical Summary
Problems solved by technology
Method used
Image
Examples
Embodiment 1
[0037] Such as figure 1 , 2 , 3, 4, 5 and 6, a cast film cutting trim processing device, including a frame 1, fixedly installed on the frame 1 to carry out trim 21 shears on the cast film 2 The cutting assembly 3 also includes a support assembly 4, a crushing assembly 5, and a transmission assembly 6. The support assembly 4 is fixedly arranged on the frame 1 and is located below the side material 21, and it includes a support for carrying out the transmission support of the side material 21. Plate 41, a hollow adsorption cavity 42 fixedly arranged under the support plate 41, and a transfer roller 43 rotatably mounted inside the adsorption cavity 42 for linear transmission of the side material 21, the transfer roller 43 is hollow, and after setting A plurality of adsorption holes 431 on its outer peripheral surface carry out the adsorption and transmission of the side material 21; the crushing assembly 5 includes a pulverizing blade 51 which passes through the support plate 41...
Embodiment 2
[0039]The inventor believes that in order to better implement the technical solution, further specific implementation methods are necessary, so the inventor describes the second embodiment on the basis of the first embodiment.
[0040] Such as figure 1 , 2 , 3, 4, 5 and 6, a cast film cutting trim processing device, including a frame 1, fixedly installed on the frame 1 to carry out trim 21 shears on the cast film 2 Cut component 3, also includes:
[0041] The support assembly 4, the support assembly 4 is fixedly arranged on the frame 1 and is located below the edge material 21, which includes a support plate 41 for supporting the edge material 21 transmission, fixedly arranged under the support plate 41 and is The suction chamber 42 arranged in hollow and the conveying roller 43 which is installed in the interior of the suction chamber 42 to carry out the linear transmission of the side material 21, the conveying roller 43 is set in hollow, and the side material is carried o...
PUM
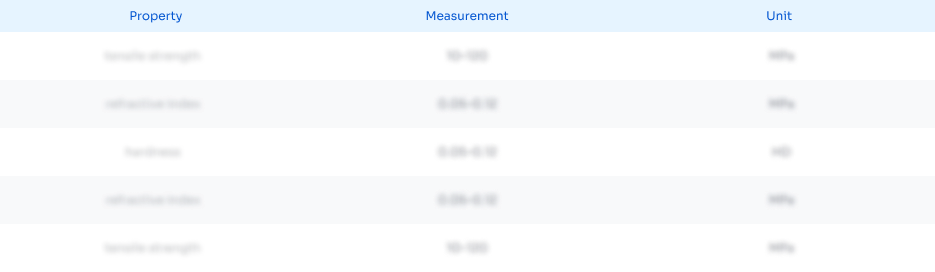
Abstract
Description
Claims
Application Information

- R&D Engineer
- R&D Manager
- IP Professional
- Industry Leading Data Capabilities
- Powerful AI technology
- Patent DNA Extraction
Browse by: Latest US Patents, China's latest patents, Technical Efficacy Thesaurus, Application Domain, Technology Topic, Popular Technical Reports.
© 2024 PatSnap. All rights reserved.Legal|Privacy policy|Modern Slavery Act Transparency Statement|Sitemap|About US| Contact US: help@patsnap.com