Flexible transporting and feeding and discharging device for robot
A robot and flexible technology, applied in the field of robot flexible transportation and loading and unloading devices, to achieve the effects of ensuring traceability, improving work efficiency, improving flexibility and working range
- Summary
- Abstract
- Description
- Claims
- Application Information
AI Technical Summary
Problems solved by technology
Method used
Image
Examples
Embodiment 1
[0048] like figure 1 As shown, this embodiment includes an automatic guided vehicle 1, a multi-axis linkage robot 2, a grabbing mechanism 31 and a body positioning tool 41. The multi-axis linkage robot 2 and the vehicle body positioning tool 41 are respectively installed on the automatic guided vehicle 1. The output end of the multi-axis linkage robot 2 is connected with a grabbing mechanism 31 , and the material grabbed onto the automatic guided vehicle 1 by the grabbing mechanism 31 is limited by the body positioning tool 41 .
[0049] like Figure 5A , Figure 5B As shown, the automatic guided vehicle 1 drives the whole of the present invention to move back and forth along the pre-laid guide magnetic strips 6 on the ground 7. The automatic guided vehicle 1 includes two drive units 101 (symmetrical left and right) and four driven To the wheels 102 (symmetric two by two). The accuracy of the overall walking of the robot is realized by the magnetic navigation sensor 108 fix...
Embodiment 2
[0056] like figure 2 As shown in the figure, the difference between this embodiment and the first embodiment is that the grabbing mechanism B32 of this embodiment is different from the grabbing mechanism A31, the vehicle body positioning tool B42 is different from the vehicle body positioning tool A41 of the first embodiment, and the utensil B52 filled with chips is Different from the vessel A51 filled with chips. Specifically:
[0057] like Figure 9 As shown, the grasping mechanism B32 of this embodiment includes a robot connecting plate 3201, a gripper cylinder B3202, a gripper B3203, a camera connecting plate 3204, a vision system 3205, a laser ranging sensor 3206, an inclination sensor 3207, and an RFID read-write head 3208 , the robot connecting plate 3201 is connected with the output end of the multi-axis linkage robot 2 through the upper flange, and a gripper cylinder B3202 is fixed under the robot connecting plate 3201, and the output ends on both sides of the grip...
Embodiment 3
[0062] like image 3 As shown, the difference between this embodiment and the first embodiment is that the grabbing mechanism C33 of this embodiment is different from the grabbing mechanism A31, the vehicle body positioning tool C43 is different from the vehicle body positioning tool 41 of the first embodiment, and the container C53 filled with chips is Different from the vessel A51 filled with chips. Specifically:
[0063] like Figure 10 As shown, the grasping mechanism C33 of this embodiment includes a robot connecting plate 3301, a positioning plate 3302, a pin 3303, a camera connecting plate 3304, a vision system 3305, a laser ranging sensor 3306, an inclination sensor 3307 and an RFID read-write head 3308. The robot connecting plate 3301 is connected with the output end of the multi-axis linkage robot 2 through the upper flange, and a positioning plate 3302 is fixed under the robot connecting plate 3301, and the positioning plate 3302 cooperates with the vessel C53 fil...
PUM
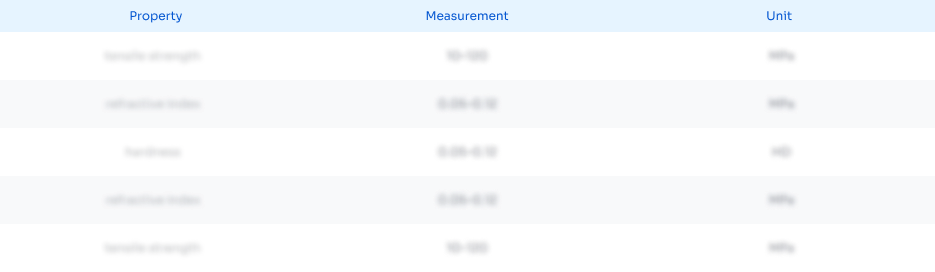
Abstract
Description
Claims
Application Information

- R&D
- Intellectual Property
- Life Sciences
- Materials
- Tech Scout
- Unparalleled Data Quality
- Higher Quality Content
- 60% Fewer Hallucinations
Browse by: Latest US Patents, China's latest patents, Technical Efficacy Thesaurus, Application Domain, Technology Topic, Popular Technical Reports.
© 2025 PatSnap. All rights reserved.Legal|Privacy policy|Modern Slavery Act Transparency Statement|Sitemap|About US| Contact US: help@patsnap.com