Hanger mechanism for adjusting parameters of UAV flight attitude angle control
A flight attitude and UAV technology, which is applied in the field of UAV flight attitude angle control parameter measurement, can solve problems such as unsatisfactory parameters, and achieve the effects of improving measurement accuracy and overcoming lift.
- Summary
- Abstract
- Description
- Claims
- Application Information
AI Technical Summary
Problems solved by technology
Method used
Image
Examples
Embodiment Construction
[0019] combine figure 1 , a hanger mechanism for controlling parameters of the flight attitude angle of a drone, comprising a vertical axis rotation mechanism, a pair of horizontal axis rotation curved guide rails, a connecting rod, and a hanger for the drone.
[0020] Referring to Fig. 2(a), the vertical axis rotation mechanism includes a pair of axial thrust bearings, a pair of axial thrust bearing support plates, a pair of arc guide rail bearing rotating shafts, a housing, and a rotating shaft. The housing is two connecting plates, which are arranged in parallel, a pair of axial thrust bearing support plates are arranged on the upper end surface, and a pair of arc guide rail bearing rotating shafts are arranged on the left and right end surfaces thereof. A pair of axial thrust bearing support plates are arranged on the upper and lower end surfaces of the housing, each axial thrust bearing support plate includes a base and a bearing groove arranged on the base, as well as th...
PUM
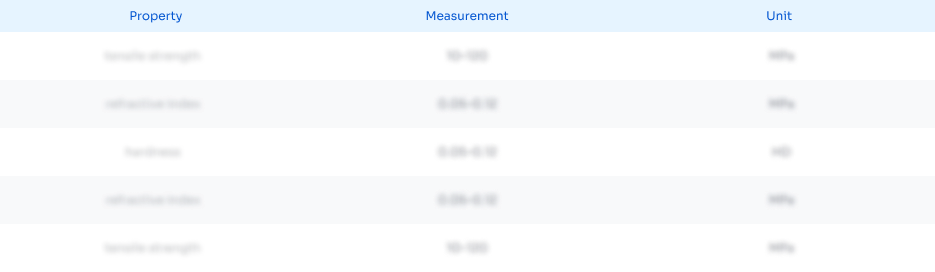
Abstract
Description
Claims
Application Information

- R&D Engineer
- R&D Manager
- IP Professional
- Industry Leading Data Capabilities
- Powerful AI technology
- Patent DNA Extraction
Browse by: Latest US Patents, China's latest patents, Technical Efficacy Thesaurus, Application Domain, Technology Topic, Popular Technical Reports.
© 2024 PatSnap. All rights reserved.Legal|Privacy policy|Modern Slavery Act Transparency Statement|Sitemap|About US| Contact US: help@patsnap.com