Preparation method and application of aspartic acid Maillard reactant
A technology of aspartic acid Maillard and Maillard reaction, which is applied in the fields of application, preparation of tobacco, food science, etc., can solve the problems of difficult to widely use cigarettes, lack of coloring ability, and single flavor of spices, etc., to improve the appearance and sensory quality, appearance and sensory quality improvement, simple and mild process conditions
- Summary
- Abstract
- Description
- Claims
- Application Information
AI Technical Summary
Problems solved by technology
Method used
Image
Examples
Embodiment 1
[0029] A preparation method of aspartic acid Maillard reactant, specifically comprising the steps of:
[0030](1) Raw material preparation: aspartic acid and reducing sugar (rhamnose and caramel, the molar ratio is 1:2) are configured in a molar ratio of 2.8:1, and the catalyst is ammonium acetate and ascorbic acid (mass ratio 1:0.5), The total mass of the catalyst accounts for 0.5% of the total mass of the Maillard reaction substrate; the mass ratio of water to the Maillard reaction substrate is 2:1;
[0031] (2) Production and preparation: first add water to the reaction tank, start the stirring motor, heat to 50°C, add aspartic acid and reducing sugar in proportion in turn, stir thoroughly until they are completely dissolved, then add the catalyst; during the reaction , set the process condition of the Maillard reaction tank as temperature 125°C, keep the stirring motor on, and the reaction time is 6h;
[0032] (3) Finished product: After the reaction, the reactant is natu...
Embodiment 2
[0035] A preparation method of aspartic acid Maillard reactant, specifically comprising the steps of:
[0036] (1) Raw material preparation: amino acids (aspartic acid and asparagine in a molar ratio of 1:1) and fermented coconut extract are used as Maillard reaction substrates, and the mass ratio of amino acids to fermented coconut extract is 2.5:1 To configure; Catalyst is ascorbic acid, ammoniacal liquor, ammonium bicarbonate (configuration by equal mass ratio), and catalyst gross mass accounts for 1% of the Maillard reaction substrate gross mass; The mass ratio of water and Maillard reaction substrate is 2.5: 1;
[0037] (2) Production preparation: first add water into the reaction tank, start the stirring motor, heat to 55°C, add amino acid and fermented coconut extract in a certain proportion in turn, stir thoroughly until completely dissolved, then add the catalyst; during the reaction , set the process condition of the Maillard reaction tank as temperature 105°C, keep...
Embodiment 3
[0042] A preparation method of aspartic acid Maillard reactant, specifically comprising the steps of:
[0043] (1) Raw material preparation: Asparagine and sugar source (3:1 by mass ratio) are used as the substrate of the Maillard reaction, and the sugar source is a composite of mannose, rhamnose, xylose, and fermented coconut extract substance (mass ratio is 1:1:1:0.6); catalyst is ammonium acetate, ascorbic acid, decanal (equal mass ratio), and the total mass accounts for 1.2% of the Maillard reaction substrate mass; water and Maillard reaction bottom The mass ratio of the substance is 2.2:1;
[0044] (2) Production preparation: first add water into the reaction tank, start the stirring motor, heat to 60°C, add asparagine and sugar source in a certain proportion in turn, stir thoroughly until completely dissolved, then add the catalyst; during the reaction , set the process condition of the Maillard reaction tank to a temperature of 98°C, keep the stirring motor on, and the...
PUM
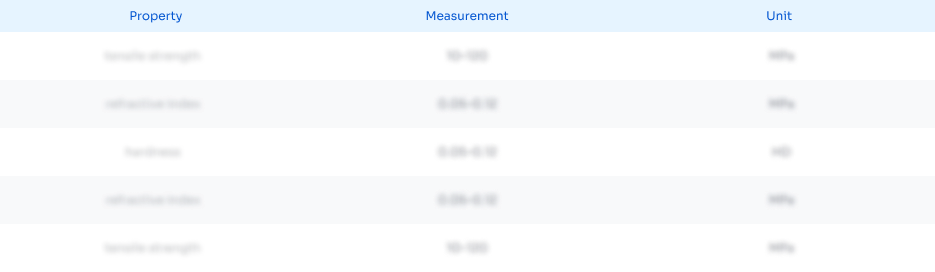
Abstract
Description
Claims
Application Information

- R&D Engineer
- R&D Manager
- IP Professional
- Industry Leading Data Capabilities
- Powerful AI technology
- Patent DNA Extraction
Browse by: Latest US Patents, China's latest patents, Technical Efficacy Thesaurus, Application Domain, Technology Topic, Popular Technical Reports.
© 2024 PatSnap. All rights reserved.Legal|Privacy policy|Modern Slavery Act Transparency Statement|Sitemap|About US| Contact US: help@patsnap.com