Polyurethane environment-friendly flame-retardant foaming material for storage battery box body assembly and preparation method thereof
A technology of foaming materials and polyurethane, which is applied in the field of battery box assembly polyurethane environmentally friendly flame-retardant foaming materials and its preparation, can solve the problems of potential safety hazards, poor flame retardancy, and short escape time for personnel, and achieve reasonable matching , high flame retardant performance, and the effect of ensuring vehicle and personal safety
- Summary
- Abstract
- Description
- Claims
- Application Information
AI Technical Summary
Problems solved by technology
Method used
Examples
Embodiment 1
[0025] A method for preparing a polyurethane environment-friendly flame-retardant foaming material for a battery box assembly, comprising the following preparation steps:
[0026] (1) Raw material treatment: Dry Liansheng polyester, polyether 4113, polyether 450 and isocyanate at a drying temperature of 40°C and a drying time of 6 hours;
[0027] (2) Weighing ratio: According to the weight ratio, weigh silicone oil: 2.5 parts, reinforced glass fiber: 180 parts, catalyst DMP-30: 1.2 parts, equilibrium catalyst HP-12: 1.3 parts, catalyst HP-54 : 1.1 parts;, flame retardant TCPP: 38 parts, water: 3.5 parts and after drying treatment, polyester: 25 parts, polyether 4113: 25 parts, polyether 450: 20 parts;
[0028] (3) Preparation of combined materials: the weighed Liansheng polyester, polyether 4113, polyether 450, silicone oil, reinforced glass fiber, catalyst DMP-30, equilibrium catalyst HP-12, catalyst HP-54, water, resistance Fuel agent TCPP is added to the reaction kettle in...
Embodiment 2
[0031] A method for preparing a polyurethane environment-friendly flame-retardant foaming material for a battery box assembly, comprising the following preparation steps:
[0032] (1) Raw material treatment: dry Liansheng polyester, polyether 4113, polyether 450 and isocyanate at a drying temperature of 40°C and a drying time of 7 hours;
[0033] (2) Weighing ratio: according to the mass ratio, weigh silicone oil: 2.75 parts, reinforced glass fiber: 215 parts, catalyst DMP-30: 1.5 parts, equilibrium catalyst HP-12: 1.5 parts, catalyst HP-54: 1.3 parts, flame retardant TCPP: 40 parts, water: 3.65 parts and dried polyester: 30 parts, polyether 4113: 30 parts, polyether 450: 27.5 parts;
[0034] (3) Preparation of combined materials: weighed Liansheng polyester, polyether 4113: 30 parts, polyether 450: 27.5 parts, silicone oil, reinforced glass fiber, catalyst DMP-30, equilibrium catalyst HP-12, catalyst Add HP-54, water, and flame retardant TCPP into the reaction kettle in turn...
Embodiment 3
[0037] A method for preparing a polyurethane environment-friendly flame-retardant foaming material for a battery box assembly, comprising the following preparation steps:
[0038] (1) Raw material treatment: dry Liansheng polyester, polyether 4113, polyether 450 and isocyanate at a drying temperature of 40°C and a drying time of 8 hours;
[0039] (2) Weighing ratio: according to the mass ratio, weigh silicone oil: 3 parts, reinforced glass fiber: 250 parts, catalyst DMP-30: 1.8 parts, balance catalyst HP-12: 1.7 parts, catalyst HP-54: 1.5 parts, flame retardant TCPP: 42 parts, water: 3.8 parts and dried polyester: 35 parts, polyether 4113: 35 parts, polyether 450: 35 parts;
[0040] (3) Preparation of combined materials: the weighed Liansheng polyester, polyether 4113, polyether 450, silicone oil, reinforced glass fiber, catalyst DMP-30, equilibrium catalyst HP-12, catalyst HP-54, water, resistance Fuel agent TCPP is added to the reaction kettle in turn and fully stirred. The...
PUM
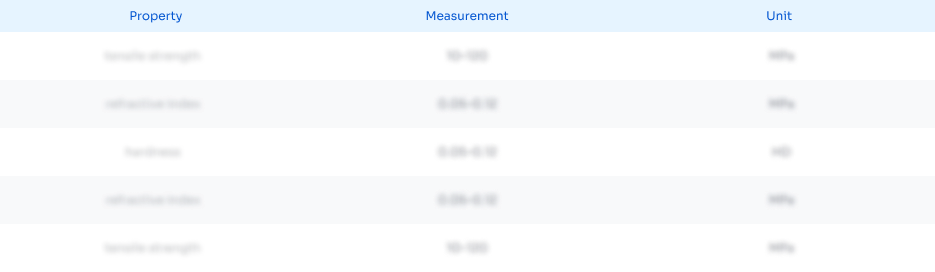
Abstract
Description
Claims
Application Information

- Generate Ideas
- Intellectual Property
- Life Sciences
- Materials
- Tech Scout
- Unparalleled Data Quality
- Higher Quality Content
- 60% Fewer Hallucinations
Browse by: Latest US Patents, China's latest patents, Technical Efficacy Thesaurus, Application Domain, Technology Topic, Popular Technical Reports.
© 2025 PatSnap. All rights reserved.Legal|Privacy policy|Modern Slavery Act Transparency Statement|Sitemap|About US| Contact US: help@patsnap.com