Deep hole machining process for five-axis machining
A processing technology and deep hole technology, applied in metal processing equipment, manufacturing tools, boring/drilling, etc., to facilitate deep hole processing, avoid collapse, and ensure quality
- Summary
- Abstract
- Description
- Claims
- Application Information
AI Technical Summary
Problems solved by technology
Method used
Examples
Embodiment
[0014] When the five-axis machine tool drills deep holes, because the drill bit is very long, the drill bit is easy to deflect, and the center of the hole is not accurate. How to solve this problem becomes the key;
[0015] Later, the plan was improved: first, a milling cutter was used to mill a hole with a diameter of 18mm deep, which played a role in guiding and fixing, and then a drill was used to drill the hole. This process was used to process the deep hole at a special position to avoid the deviation of the hole position. At the same time, it can ensure uniform pore size and improve product quality;
[0016] In the actual drilling process, in order to facilitate chip removal, the drill bit exits the workpiece every 5mm and then drills until the end. This operation method is original, although it can guarantee the accuracy of the hole diameter and hole position.
PUM
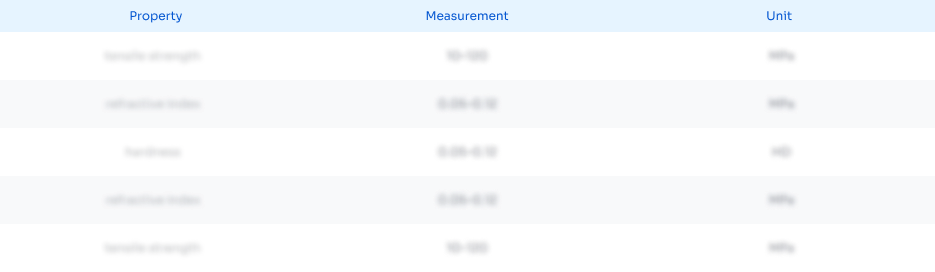
Abstract
Description
Claims
Application Information

- R&D Engineer
- R&D Manager
- IP Professional
- Industry Leading Data Capabilities
- Powerful AI technology
- Patent DNA Extraction
Browse by: Latest US Patents, China's latest patents, Technical Efficacy Thesaurus, Application Domain, Technology Topic, Popular Technical Reports.
© 2024 PatSnap. All rights reserved.Legal|Privacy policy|Modern Slavery Act Transparency Statement|Sitemap|About US| Contact US: help@patsnap.com