Rigid-flexible mixed three-dimensional force perception mechanism
A three-dimensional force, rigidity and flexibility technology, applied in the field of sensors, can solve the problems of maintaining the same and unable to maintain the mapping relationship between the input and output of the sensor, and achieve the effect of simple structure, convenient manufacturing, and convenient serial production.
- Summary
- Abstract
- Description
- Claims
- Application Information
AI Technical Summary
Problems solved by technology
Method used
Image
Examples
Embodiment Construction
[0014] exist figure 1 In the three-dimensional schematic diagram of the rigid-flexible mixed three-dimensional force sensing mechanism shown, the mechanism mainly includes an upper platform 2, a lower platform 1 and three deformable force-measuring branches connecting the upper and lower platforms. The lower platform is a fixed platform, near its edge there are three contour support columns distributed in an equilateral triangle. 9 is arranged between the three edge support columns 3 and the center support column, and each of them is connected with a deformable force-measuring branch. The three force-measuring branches are made up of a sensor assembly, a first moving pair 8, a first rotating pair 12, a second rotating pair 14 and a first universal winch 16, as figure 2 shown. A sensor assembly is arranged between the two parallel guide rails, which mainly includes: a sensor, a sensor connector 18 , a sensor fixed connection frame 6 , a sensor fixed support frame 7 , a guide...
PUM
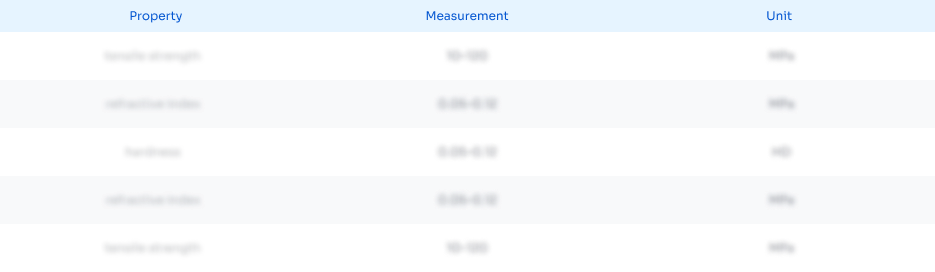
Abstract
Description
Claims
Application Information

- Generate Ideas
- Intellectual Property
- Life Sciences
- Materials
- Tech Scout
- Unparalleled Data Quality
- Higher Quality Content
- 60% Fewer Hallucinations
Browse by: Latest US Patents, China's latest patents, Technical Efficacy Thesaurus, Application Domain, Technology Topic, Popular Technical Reports.
© 2025 PatSnap. All rights reserved.Legal|Privacy policy|Modern Slavery Act Transparency Statement|Sitemap|About US| Contact US: help@patsnap.com