A kind of papermaking process of secondary pulp external glue water writing paper
A process and glue technology, which is applied in the field of secondary pulp externally glued water writing paper copying process, can solve the problems of increasing environmental protection costs, achieve the effects of saving wood, facilitating industrialized mass production, and solving the problem of unable to print dots and read codes
- Summary
- Abstract
- Description
- Claims
- Application Information
AI Technical Summary
Problems solved by technology
Method used
Examples
Embodiment 1
[0045] A kind of papermaking process of water-based paper with external glue applied to secondary pulp, comprising the following steps:
[0046] Step 1: Soak commercial wood pulp, straw pulp, and bamboo pulp in pulp tanks for 1 to 3 hours, make them fully absorb water and disperse, then dehydrate, wash, and sieve impurities before entering the next process; the straw pulp is either straw pulp or wheat straw pulp;
[0047] Step 2: Perform beating treatment on the pulp after dehydration, washing, and sieving of impurities in the form of free long fiber beating, with a beating degree of 20° to 24°, to obtain qualified papermaking pulp;
[0048] Step 3: Input the obtained qualified slurry into the high-frequency deflaking machine for deflaking;
[0049] Step 4: Obtain qualified papermaking pulp after mixing the decomposed wood pulp, straw pulp and bamboo pulp;
[0050] Step 5: Use the qualified papermaking pulp to make paper with a sandwich paper machine. The pulp flow is sent t...
Embodiment 2
[0055] A kind of papermaking process of water-based paper with external glue applied to secondary pulp, comprising the following steps:
[0056] Step 1: Soak commercial wood pulp, straw pulp, and bamboo pulp in pulp tanks for 1 to 3 hours, make them fully absorb water and disperse, then dehydrate, wash, and sieve impurities before entering the next process; the straw pulp is either straw pulp or wheat straw pulp;
[0057] Step 2: Perform beating treatment on the pulp after dehydration, washing, and sieving of impurities in the form of free long fiber beating, with a beating degree of 20° to 24°, to obtain qualified papermaking pulp;
[0058] Step 3: Input the obtained qualified slurry into the high-frequency deflaking machine for deflaking;
[0059] Step 4: Obtain qualified papermaking pulp after mixing the decomposed wood pulp, straw pulp and bamboo pulp;
[0060] Step 5: Use the qualified papermaking pulp to make paper with a sandwich paper machine. The pulp flow is sent to ...
Embodiment 3
[0065] A kind of papermaking process of water-based paper with external glue applied to secondary pulp, comprising the following steps:
[0066] Step 1: Soak commercial wood pulp, straw pulp, and bamboo pulp in pulp tanks for 1 to 3 hours, make them fully absorb water and disperse, then dehydrate, wash, and sieve impurities before entering the next process; the straw pulp is either straw pulp or wheat straw pulp;
[0067] Step 2: Perform beating treatment on the pulp after dehydration, washing, and sieving of impurities in the form of free long fiber beating, with a beating degree of 20° to 24°, to obtain qualified papermaking pulp;
[0068] Step 3: Input the obtained qualified slurry into the high-frequency deflaking machine for deflaking;
[0069] Step 4: Obtain qualified papermaking pulp after mixing the decomposed wood pulp, straw pulp and bamboo pulp;
[0070] Step 5: Use the qualified papermaking pulp to make paper with a sandwich paper machine. The pulp flow is sent t...
PUM
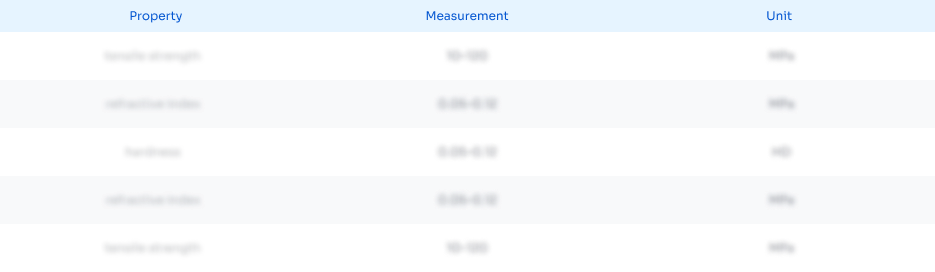
Abstract
Description
Claims
Application Information

- R&D
- Intellectual Property
- Life Sciences
- Materials
- Tech Scout
- Unparalleled Data Quality
- Higher Quality Content
- 60% Fewer Hallucinations
Browse by: Latest US Patents, China's latest patents, Technical Efficacy Thesaurus, Application Domain, Technology Topic, Popular Technical Reports.
© 2025 PatSnap. All rights reserved.Legal|Privacy policy|Modern Slavery Act Transparency Statement|Sitemap|About US| Contact US: help@patsnap.com