A Step Temperature Compensation Method for Crystal Oscillator
A crystal oscillator and temperature compensation technology, which is applied in the direction of electrical components, output stability, etc., can solve the problems of temperature sensor and resonant chip temperature hysteresis, failure to make a breakthrough, limited compensation accuracy, etc., to achieve easy integration and mass production, easy Real-time high-precision compensation, good compensation effect
- Summary
- Abstract
- Description
- Claims
- Application Information
AI Technical Summary
Problems solved by technology
Method used
Image
Examples
Embodiment Construction
[0040] Specific embodiments of the present invention will be described below in conjunction with the accompanying drawings, so that those skilled in the art can better understand the present invention. It should be noted that in the following description, when detailed descriptions of known functions and designs may dilute the main content of the present invention, these descriptions will be omitted here.
[0041] image 3 It is a specific implementation flowchart of the step temperature compensation method of the crystal oscillator of the present invention.
[0042] In this example, if image 3 As shown, the step temperature compensation method of the crystal oscillator of the present invention comprises the following steps:
[0043] Step S1: Determine the target frequency f 0 Corresponding binary code B 0i
[0044] at room temperature T 0 , such as at 25°C, adjust the control voltage of the voltage-controlled crystal oscillator, that is, the voltage control terminal of...
PUM
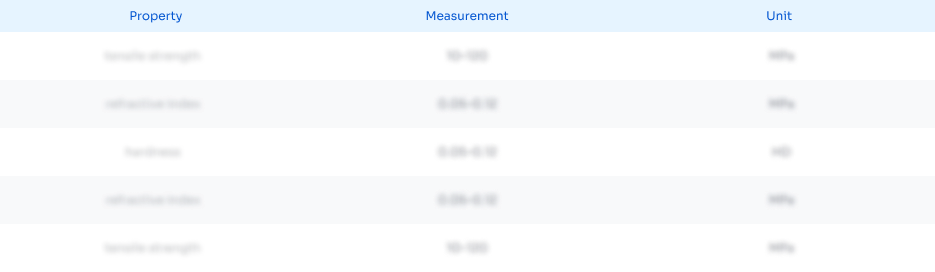
Abstract
Description
Claims
Application Information

- R&D
- Intellectual Property
- Life Sciences
- Materials
- Tech Scout
- Unparalleled Data Quality
- Higher Quality Content
- 60% Fewer Hallucinations
Browse by: Latest US Patents, China's latest patents, Technical Efficacy Thesaurus, Application Domain, Technology Topic, Popular Technical Reports.
© 2025 PatSnap. All rights reserved.Legal|Privacy policy|Modern Slavery Act Transparency Statement|Sitemap|About US| Contact US: help@patsnap.com