Precise forging method for engineering machine connecting rod
A technology of precision forging and engineering machinery, applied in the field of precision forging of engineering machinery connecting rods, can solve the problems of large forging machining allowance and material consumption, and achieve the effects of less uniform processing, cost reduction, and stable tolerances.
- Summary
- Abstract
- Description
- Claims
- Application Information
AI Technical Summary
Problems solved by technology
Method used
Image
Examples
Embodiment 1
[0015] Such as figure 2 The engineering machinery connecting rod shown has a large connecting rod end and a small connecting rod end connected by rods, and holes are respectively arranged on the large connecting rod end and the small connecting rod end;
[0016] The precision forging method of the engineering machinery connecting rod comprises the following steps:
[0017] A. The billet is heated at a temperature of 1180°C to 1200°C;
[0018] B. Place the billet in the cavity of the rod drawing die to elongate the rod, and then place it in the cavity of the first forging die to forge a rough forging, such as figure 1 shown;
[0019] C. Place the forging rough blank in the cavity of the second forging die to forge the forging, such as figure 2 shown;
[0020] D. Trimming, deburring and shot blasting of forgings;
[0021] E. Place the forging in the cavity of the correcting precision pressing forging die for calibration and precision pressing, and the temperature is 500°C...
Embodiment 2
[0023] A precision forging method for an engineering machinery connecting rod, comprising the following steps:
[0024] A. The billet is heated at a temperature of 1180°C to 1200°C;
[0025] B. Place the billet in the cavity of the rod drawing die to elongate the rod, and then place it in the cavity of the first forging die to forge a rough forging, such as figure 1 shown;
[0026] C. Place the forging rough blank in the cavity of the second forging die to forge the forging, such as figure 2 shown;
[0027] D. Trimming, deburring and shot blasting of forgings;
[0028] E. Place the forging in the cavity of the calibrated sizing forging die for calibration and sizing, and the temperature is 500°C to complete the precision forging of the engineering machinery connecting rod; other features are the same as in Embodiment 1.
PUM
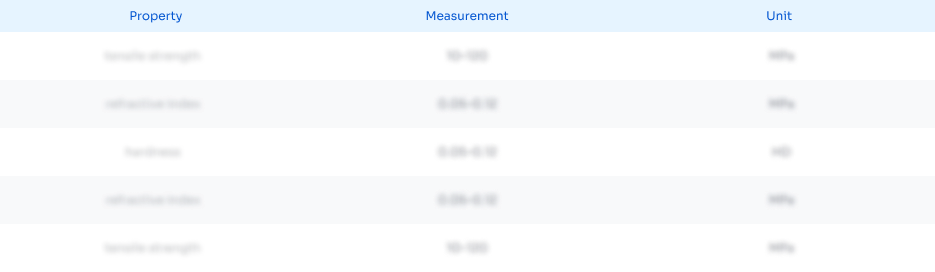
Abstract
Description
Claims
Application Information

- R&D
- Intellectual Property
- Life Sciences
- Materials
- Tech Scout
- Unparalleled Data Quality
- Higher Quality Content
- 60% Fewer Hallucinations
Browse by: Latest US Patents, China's latest patents, Technical Efficacy Thesaurus, Application Domain, Technology Topic, Popular Technical Reports.
© 2025 PatSnap. All rights reserved.Legal|Privacy policy|Modern Slavery Act Transparency Statement|Sitemap|About US| Contact US: help@patsnap.com