Dry distillation method of connecting Ramsbottom carbon dry distillation furnace with double-section gasification furnace and using high-temperature coal gas to replace combustion supporting gas
A technology for a dry distillation furnace and a gasifier, which is applied to the field of high-temperature gas in the connection of a blue carbon dry distillation furnace and a double-stage gasifier to replace the auxiliary gas dry distillation, and can solve the problems of high separation cost and reduction of the use value of the gas released by the dry distillation coal.
- Summary
- Abstract
- Description
- Claims
- Application Information
AI Technical Summary
Problems solved by technology
Method used
Image
Examples
Embodiment Construction
[0042] The present invention will be further described according to the accompanying drawings.
[0043] The semi-coke carbonization furnace is connected with the high-temperature gas of the double-stage gasifier to replace the gas-assisted carbonization method. The specific steps are as follows:
[0044] The gas at 550-850°C in the lower section of the double-stage gas generator passes through the bushing hole 7, or the nitrogen-free gas enters the combustion chamber 13 of the semi-coke retort furnace after passing through the high-efficiency heat preservation dust collector 11;
[0045] Will The 550-850°C coal gas or nitrogen-free coal gas entering the combustion chamber 13 of the semi-coke retort furnace is evenly taken into the retort chamber 15 of the semi-coke retort furnace through a plurality of jet holes 14 of the original combustion chamber;
[0046] according to 550-850 ℃ gas or nitrogen-free gas enters the dry distillation semi-coke furnace to dry bitumino...
PUM
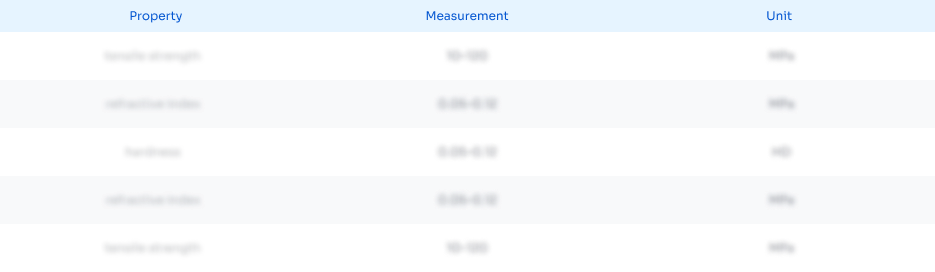
Abstract
Description
Claims
Application Information

- R&D
- Intellectual Property
- Life Sciences
- Materials
- Tech Scout
- Unparalleled Data Quality
- Higher Quality Content
- 60% Fewer Hallucinations
Browse by: Latest US Patents, China's latest patents, Technical Efficacy Thesaurus, Application Domain, Technology Topic, Popular Technical Reports.
© 2025 PatSnap. All rights reserved.Legal|Privacy policy|Modern Slavery Act Transparency Statement|Sitemap|About US| Contact US: help@patsnap.com