Single crystal combined raw material moulding technological design with high loading density
A molding process and high-filling technology, which is applied in the directions of single crystal growth, single crystal growth, polycrystalline material growth, etc., can solve the problems affecting the standardization of single crystal growth process, poor process parameter reproducibility, and affecting the quality of single crystal, etc., to achieve The effect of promoting standardized operation, rational and scientific design process, and significant social and economic benefits
- Summary
- Abstract
- Description
- Claims
- Application Information
AI Technical Summary
Problems solved by technology
Method used
Examples
Embodiment
[0014] The design steps of high packing density combined raw material molding process are as follows:
[0015] 1) Draw a three-dimensional view of the inner wall of the crucible, 2) Calculate the theoretical volume of the crucible, 3) Analyze the physical properties of the single crystal material, 4) Determine the weight of the single crystal raw material that needs to be filled, 5) Confirm the three-dimensional split method of the inner space of the crucible, 6) Test Single crystal raw material powder molding parameters and establishment of database, 7) confirmation of molding process plan and process calculation, 8) selection of mold type, 9) selection of molding equipment, 10) preparation of molding process card.
[0016] Further, in step 3, the physical properties of the sapphire single crystal raw material alumina are analyzed and the alumina melt density and thermal expansion coefficient are determined as the key influencing factors.
[0017] Further, in step 4, the maxi...
PUM
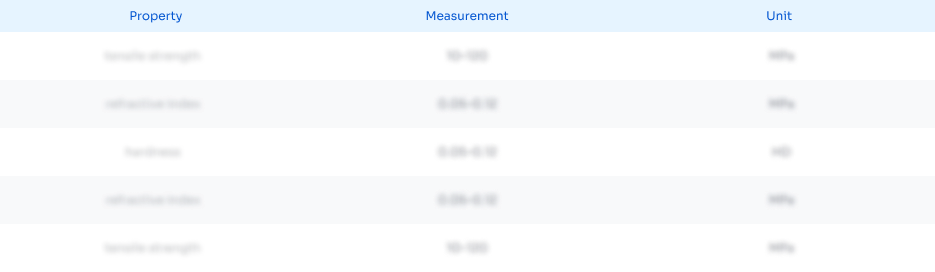
Abstract
Description
Claims
Application Information

- Generate Ideas
- Intellectual Property
- Life Sciences
- Materials
- Tech Scout
- Unparalleled Data Quality
- Higher Quality Content
- 60% Fewer Hallucinations
Browse by: Latest US Patents, China's latest patents, Technical Efficacy Thesaurus, Application Domain, Technology Topic, Popular Technical Reports.
© 2025 PatSnap. All rights reserved.Legal|Privacy policy|Modern Slavery Act Transparency Statement|Sitemap|About US| Contact US: help@patsnap.com