Lower die of bearing seat precoated sand die
A technology of coated sand and bearing seats, which is applied in the direction of manufacturing tools, casting molding equipment, casting molds, etc., can solve problems such as complex structures and shapes, achieve the effects of reducing casting defects, realizing automatic production, and improving yield
- Summary
- Abstract
- Description
- Claims
- Application Information
AI Technical Summary
Problems solved by technology
Method used
Image
Examples
Embodiment Construction
[0024] In order to further illustrate the technical solution of the present invention, the specific implementation manner of the present invention is now described in conjunction with the accompanying drawings, as Figure 1 to Figure 4 , according to the design drawing of the bearing seat, in this example, a small bearing seat is taken as an example, the number of bearing seats is selected to be four, and the number of bearing seats is evenly distributed, and the outer dimension of the bearing seat is enlarged by 8-12 mm to make a coated sand mold for the bearing seat , in this example, the horizontal central plane of the bearing seat is selected as the pouring parting surface, and the parting surface is used as the boundary, and the upper mold 1 and the lower mold 2 are respectively made by the coated sand mold of the bearing seat centered on the parting surface of the bearing seat; On the upper mold 1, in this example, a steel plate with a thickness of 50 mm is used as the up...
PUM
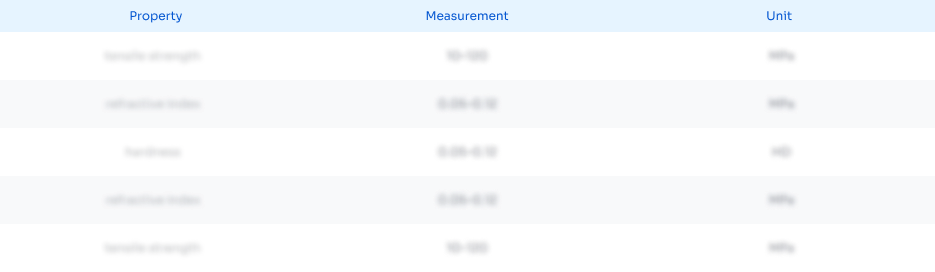
Abstract
Description
Claims
Application Information

- Generate Ideas
- Intellectual Property
- Life Sciences
- Materials
- Tech Scout
- Unparalleled Data Quality
- Higher Quality Content
- 60% Fewer Hallucinations
Browse by: Latest US Patents, China's latest patents, Technical Efficacy Thesaurus, Application Domain, Technology Topic, Popular Technical Reports.
© 2025 PatSnap. All rights reserved.Legal|Privacy policy|Modern Slavery Act Transparency Statement|Sitemap|About US| Contact US: help@patsnap.com