Permanent magnetic rigidity variable drive module for flexible robot
A driving module and robot technology, which is applied in the field of flexible robots, can solve the problems of insufficient rigidity change ability of flexible robots, reduce the mass and inertia of the operating arm, etc., and achieve the effect of light weight, reduced mass and inertia, and a wide range of applications
- Summary
- Abstract
- Description
- Claims
- Application Information
AI Technical Summary
Problems solved by technology
Method used
Image
Examples
Embodiment
[0022] combine figure 1 , figure 2 and image 3 Describe this embodiment, this embodiment comprises: rope winch 2, fixed pulley A9, movable pulley 10, rope 16, fixed pulley B17, and described rope 16 one end is fixed on rope winch 2 and then passes through fixed pulley A9, movable pulley 19, fixed pulley successively. Pulley B17, described rope winch 2, fixed pulley A9, fixed pulley B17 are circumscribed on the same straight line, and described movable pulley 10 is clamped on the symmetrical axis of fixed pulley A9 and fixed pulley B17.
[0023] The rope 16 in the present invention is a rope made of a soft steel wire rope or other soft materials that can only be bent but cannot be stretched axially;
[0024] The invention is a permanent magnet variable stiffness flexible robot driving module with simple motion form, simple manufacture and simple operation;
[0025] This embodiment is a further limitation of Embodiment 1. In this embodiment, the rope winch 2 is a winch shaf...
PUM
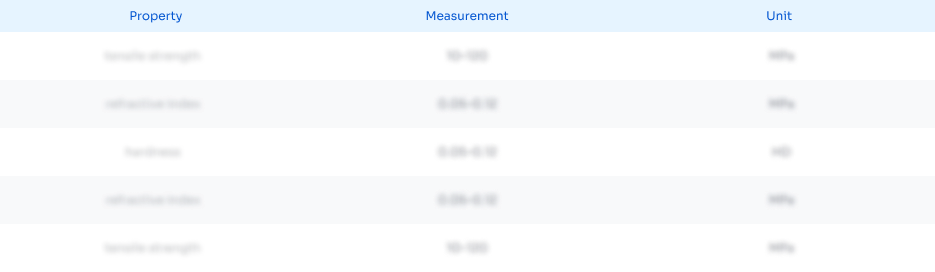
Abstract
Description
Claims
Application Information

- Generate Ideas
- Intellectual Property
- Life Sciences
- Materials
- Tech Scout
- Unparalleled Data Quality
- Higher Quality Content
- 60% Fewer Hallucinations
Browse by: Latest US Patents, China's latest patents, Technical Efficacy Thesaurus, Application Domain, Technology Topic, Popular Technical Reports.
© 2025 PatSnap. All rights reserved.Legal|Privacy policy|Modern Slavery Act Transparency Statement|Sitemap|About US| Contact US: help@patsnap.com